The Vanadium Redox Battery for Emergency
Back-Up Applications
M. Skyllas-Kazacos and C. Menictas
School of Chemical Engineering and Industrial Chemistry
The University of New South Wales, Sydney AUSTRALIA.
email: M.Kazacos@unsw.edu.au
Abstract
Secure and reliable power is essential in areas such as telecommunications and
information technology to safeguard the vast computer networks which have been
established. Uninterruptable power systems have incorporated battery technology
to allow smooth power feeding switch-over in the case of a power failure. In
such systems lead-acid batteries have commonly been used until generators come
on-line or for safe computer shutdown.
A new battery system, the Vanadium Redox Battery (VRB) is under development at
the University of New South Wales which provides many advantages over
conventional batteries for emergency back-up applications. This system stores
all energy in the form of liquid electrolytes which are recirculated around the
battery system. The electrolytes can be recharged an indefinite number of times,
or the system can be instantly recharged by mechanically exchanging the
discharged solution with recharged solution.
A vanadium battery emergency back-up system has been designed and tested for
operation between a restricted voltage operating range of 22-28V. The system
achieved energy efficiencies above 80% and coulombic and voltage efficiencies as
high as 96.4% and 92.2% respectively depending on the load.
The system demonstrated excellent performance characteristics with a capacity
utilisation up to 94% of theoretical.
1. Introduction
While the development of new efficient and environmentally safe energy storage
systems has been a critical issue for the more widespread use of renewable
energies such as solar and windpower, the availability of safe and reliable
batteries for emergency back-up applications would provide enormous benefits in
the rapidly growing area of telecommunications and information technology.
Uninterruptable Power Systems (UPS) are widely used in the telecommunication and
financial industries where secure power for vital computer installations and
electrical equipment is a top priority. These systems rely on sealed lead-acid
batteries to provide 10-15 minutes of power in the case of power failure,
enabling an orderly shutdown of computer systems, or allowing sufficient time
for a diesel generator to switch on.
Many problems are regularly encountered in the use of diesel generators,
however, these problems often arising from failure of the generators to switch
on due to flat starter battery problems.
The new vanadium redox flow battery currently under development at the
University of New South Wales has many unique features which would make it ideal
for emergency back-up applications, particularly as a diesel generator
replacement which could also be integrated into the UPS system itself. The
features and operating principles of the vanadium redox battery (VRB) are
discussed below:
2. Basic Principles and Features of the VRB
The vanadium redox battery which was pioneered at the University of NSW, was
proposed to overcome the deficiencies of other energy storage systems. Briefly,
the VRB employs V(II)/V(III) and V(IV)/V(V) redox couples in the negative and
positive half-cell electrolytes therefore, there are no problems of
cross-contamination and the solutions have an indefinite life [1-3]. Additional
features of the vanadium battery which would make it ideally suited for a wide
range of energy storage applications[4,5] are given in Table 1 while a schematic
diagram of the system is given in Figure 1.
In the vanadium redox cell, the following half-cell reactions are involved:
At the negative electrode:
V3+ + e - <----> V 2+ E0 =
-0.26V (1)
At the positive electrode:
VO2+ + 2H+ + e- <----> VO2+
+ H2O E0 = 1.00V (2)
The standard cell potential is thus E0 cell = 1.26 Volts at
concentrations of 1 mole per litre and at 250C. Under actual cell
conditions, an open circuit voltage of 1.4 Volts is observed at 50% state of
charge, while a fully charged cell produces over 1.6 Volts at open-circuit. The
electrolyte for the vanadium battery is 2M vanadium sulphate in 2.5M H2SO4, the
vanadium sulphate (initially 1M V(III) + 1 M V(IV) being prepared by chemical
reduction or electrolytic dissolution of V2O5 powder[6]. The basic components of
the redox cell are illustrated in Figure 2.
Table 1. Benefits of Vanadium Redox Battery for Large Scale Energy Storage.

Energy stored in tanks separate from the cell stack
- System capacity can be readily increased by adding more solution.
- Cost per kWh decreases as energy storage capacity increases.
- Can save land space by building underground electrolyte storage tanks.
- Greater safety since less risk of instantaneous mixing of electrolytes and
sudden release of energy. As solutions are pumped through cell stack, can
act as coolants allowing better heat exchange and reducing thermal
management problems.
Uses vanadium solution in bath half-cells
- Cross-mixing of electrolytes across membrane does not lead to
contamination of electrolytes.
- Solutions have indefinite life so that replacement costs are low (only
battery stacks would need replacement at the end of their life).
- Indefinite life of solutions means that they can be continuously recycled
so that there are no waste disposal problems. Vanadium redox couples are
electrochemically reversible so that high energy efficiencies are possible.
- Can be recharged at high rates at a fraction of the time needed for the
lead acid battery.
- Vanadium is readily available and relatively low cost, so that
manufacturing or capital costs are low.
Same solution pumped through each cell in stack
- Every cell is at the same state of charge.
- System monitoring and maintenance is simple since each individual cell
does not need to be carefully controlled and adjusted.
- By monitoring electrolyte state of charge can accurately determine
capacity of battery.
- Cells can be stacked in series and parallel.
- Trim cells can be used to adjust voltage as required.
- Does not require overcharging for cell equalisation so minimises hydrogen
explosion hazard.

After selecting the most suitable electrode and membrane materials from
small-scale cell test results, their performance in larger prototype
batteries has been evaluated under continuous long-term cycling over a wide
range of operating conditions.
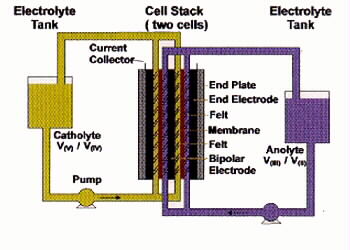
Fig 1. Schematic of UNSW Vanadium Redox Battery[7].
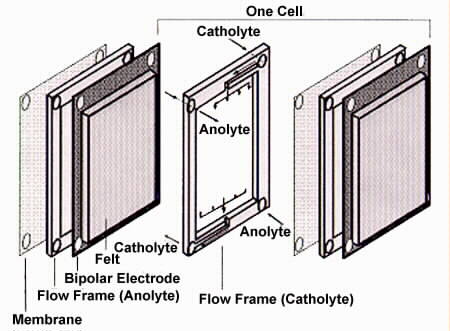
Fig 2. Components of the Redox Cell[7].
The vanadium battery is now at a relatively advanced stage of development
with several 1-3 kW prototype batteries already constructed and tested both
as emergency back-up batteries and in an electric golf-cart at UNSW. Overall
energy efficiencies as high as 90% have been achieved to date, not including
shunt current and pumping energy losses. These have been estimated at 2-3%,
so that even at 87-88% overall energy efficiency, the vanadium battery is
proving to be one of the most efficient energy storage systems currently
under development.
In addition to the technical benefits described in Table 1, other features
include:
- Do not involve complex solid phase changes during charging and discharging
which lead to shedding or shorting in conventional batteries.
- Can be fully discharged without harm to battery.
- Shelf life is theoretically unlimited.
- It is possible to charge a battery at 2 volts and discharge at 100 volts
without affecting battery life or performance.
- Possibility of mechanical or “instant recharge” by replacing
electrolytes.
Redox cell batteries[8] are thus the only type of battery systems which
offer the possibility of efficient “instant recharge”. Although the
aluminium/air and zinc slurry/air systems allow mechanical recharge, in both
cases the recycling of the active materials is much more complicated and
energy inefficient (e.g. the Hall-Heroult process for producing metallic
aluminium has less than 50% energy efficiency). Unlike other batteries
therefore, the vanadium battery can be both electrically recharged and
mechanically recharged.
3. Advantages of Vanadium Redox Battery for Emergency Back-Up
Applications
Many UPS systems employ lead-acid batteries with or without a diesel
generator. Due to the poor performance and short cycle life of the lead-acid
battery under deep discharge cycling, there is a heavy dependence on the
diesel generator for longer term power generation in the event of power
failure. With a low cost, efficient battery, however, considerable reduction
or complete replacement of the diesel generator could be possible in the
near future.
The important features of the vanadium battery for this application are:
- Low cost for large storage capacities. Cost per kWh decreases as energy
storage capacity increases, typical projected battery costs for 8 or more
hours of storage being as low as US$150 per kWh.
- Existing systems can be readily upgraded and additional storage capacity
can be easily installed by changing the tanks and volumes of electrolyte.
- The charge and discharge voltage of the battery stack can be chosen by
introducing tapped cells. This provides the opportunity to change the
operating conditions so as to protect sensitive equipment from large voltage
fluctuations and allow operation within a narrow voltage window for charging
and discharging.
- Capacity and state-of-charge of the system can be easily monitored, by
employing an open-circuit cell.
- Easy maintenance
- Flexibility
4. Performance of Vanadium Redox Battery in Emergency Back-Up
System
A VRB emergency back-up battery was recently designed and built to meet the
desired operating conditions specified by the Department of Defence. Its
intent was to allow a comparison with the current nickel/cadmium system
employed as a back-up battery. The primary requirements for the VRB Defence
system were that it should be charged between 5% and 95% of its rated
capacity while remaining in the voltage range of 22 V to 28 V under loads of
0 to 160 A. The capacity of the current nickel/cadmium system was 160 Ahr,
therefore, the VRB Defence battery was designed to meet and preferably
exceed this capacity, even at high constant loads.
The vanadium redox battery defence system shown in Figure 3, comprises of 2
battery stacks each containing 19 cells with a tapping cell placed at cell
No.17 in each stack.
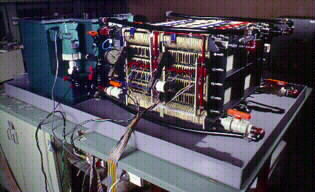
Fig 3. Vanadium Redox Battery Defence Emergency Back-Up
System.
The system also uses a small external cell which gives the open-circuit
voltage between the positive and negative electrolytes. The electrolyte
storage tanks are made from impact resistant plastic and the volume of
electrolyte employed is 83 L per half-cell series. The two tanks share a
common wall to separate them. An anti-syphoning balance pipe is incorporated
in the tanks to allow any solution passing the fill limit of one tank to
flow back into its place of origin in the adjacent tank. This allows over
design to be minimised, while ensuring that a high safety and reliability
level is maintained in the system's components.
The design of the VRB Defence battery required 2 stacks comprising of 19
cells each to be electrically connected in parallel. Each stack contains a
tapping cell at cell no.17 which also must be taken into consideration when
the electrical connection is made.
Battery Stack 1 contains conducting plastic electrodes and unactivated
graphite felt. The membrane used in this battery is Selemion AMV membrane
(Asahi Glass, Japan). The battery was connected to all the system components
in order to make a functioning VRB battery system employing only one stack.
This battery was then tested at various currents to determine its
performance. Table 2 summarises the efficiencies obtained at various
constant charge/discharge currents.
The efficiencies shown in Table 2 were not as high as expected and this is
mainly due to the lower than expected voltage efficiencies due to the use of
unactivated felt and the AMV membrane.
Table 2 Efficiencies for Stack 1 at various constant charge/discharge
currents.
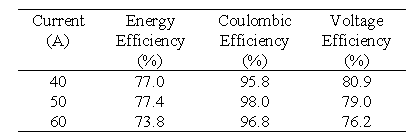
The average cell resistance was calculated by carrying out a polarisation
test on the battery. The battery is first charged to a 50% state of charge
(SOC) before the test is carried out. Once this level is reached the battery
is charged and discharged for 1 min time intervals at different currents as
shown in Table 3.
Table 3 Polarisation test results for Stack 1 performed at a stack
open-circuit voltage of 25.8V at approximately 50% state of charge.
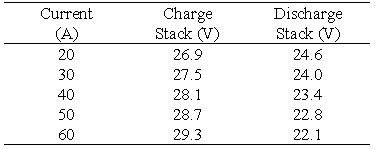
From the slope of the voltage versus current curves the average cell area
resistivities during charging and discharging were calculated as 4.74 ohms
cm2 and 4.89 ohms cm2 respectively. From the cell resistivities it is
evident that the low voltage efficiencies obtained are the result of a
higher than expected average cell resistivity. The major physical
contributors to the cell resistivity are the electrodes and membranes. In
this particular battery the majority of electrode resistivities are between
0.7 - 1.3 ohms cm2 and the Selemion AMV membrane has a resistivity rating
between 1.5 - 3.0 ohms cm2. This resistivity can vary in production batches
therefore a major contributor to the cell resistivity obtained is the
membrane. With constant cycling, battery efficiency improves however, the
measurement of cell area resistivity early in the battery's life establishes
an area resistivity value that is not significantly influenced by battery
cycle history.
The second battery stack in the VRB Defence project employed a second type
of conducting plastic electrode and graphite felt. A tapping cell is
incorporated at cell no.17 and the membrane employed was the experimental
New Selemion Type II membrane (Asahi Glass, Japan) which has an area
resistivity in the vicinity of 1 cm2. This battery stack was connected to
the rest of the vanadium battery system. The stack was then tested at
various constant charge/discharge currents with the efficiencies obtained
presented in Table 4.
The energy efficiency obtained with this battery at 60 A is markedly higher
than with Stack 1 ie. 78.3 compared with 73.8%. As the battery becomes
conditioned, however the efficiency is seen to improve. Three 100 A cycles
were carried out continuously, to test the behaviour of the battery. It is
important to observe, that with each cycle the coulombic efficiency, the
voltage efficiency, and the energy efficiency all increase steadily.
Table 4 Efficiencies for Stack 2 at various constant charge/discharge
currents.
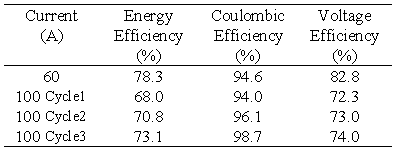
A polarisation test was performed on Stack 2 to ascertain the average cell
resistance in the battery with the polarisation test results shown in Table
5.
Table 5 Polarisation test results for Stack 2 performed at a stack
open-circuit voltage of 26.3V at approximately 50% state of charge.
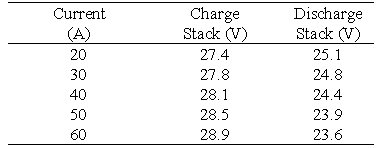
The average cell area resistivities calculated from the data in Table 5 were
2.90 ohms cm2 for charging and 3.13 ohms cm2 for discharging. These area
resistivities obtained are significantly lower than for stack 1 due to the
use of the lower resistance New Selemion membrane. As such, the battery
possesses higher overall energy efficiencies which are expected to improve
with further cycling of the battery.
Two-Stack Battery Performance Analysis The performance of the VRB Defence
battery system was tested under 2 main operating modes. The first involved
utilisation of all cells in the battery system. This was required for the
determination of overall efficiencies, resistance measurements and
self-discharge tests. The second mode utilised the tapping cells, for
example charging the battery system across 17 cells and discharging the
battery system across 19 cells. This mode was used in tests that required
the battery voltage to be maintained within specified voltage limits.
The efficiency of the battery system was investigated in a current range of
40 - 120 A with the upper current of 120 A being the maximum deliverable
current from the power supply. Table 6 below summarises the efficiencies
obtained at each current. In this test series the charge and discharge
currents were constant at each respective current and for the duration of
each test cycle.
Table 6 Total battery efficiencies at various constant charge/discharge
currents.
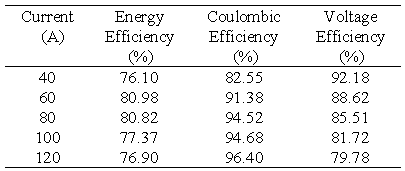
The results presented in Table 6 are also plotted in Figure 4. Figure 4
shows that as expected, coulombic efficiency increases and voltage
efficiency decreases with increasing current giving a maximum overall energy
efficiency of over 80% in the current range of 60-80 amps.
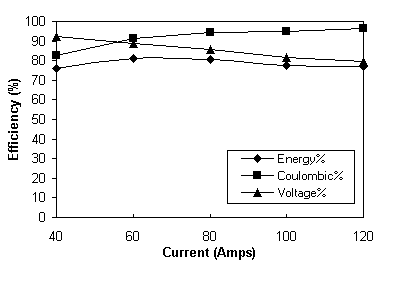
Fig. 4 Total battery efficiency profiles.
A typical voltage profile for the stack voltage during charging and
discharging at 100 A and the corresponding OCV stack voltage profile is
illustrated in Figure 5. The OCV profile of Figure 5 shows the stack voltage
for zero current flow and thus represents the ideal voltage path with zero
losses. The actual stack voltage, however, contains deviations from ideality
due to the resistance and polarisation losses in the battery. A higher
voltage is thus needed during the charging phase and a lower voltage is
available during the discharge phase. It is therefore important that the
resistance of the battery system be minimised, to allow maximum utilisation
of the available energy.
The internal resistances of the individual batteries were calculated as
described above and a polarisation test was also carried out to determine
the resultant overall resistance for the 2 stack battery which is both
hydraulically and electrically connected. The resulting polarisation plot is
illustrated in Figure 6.
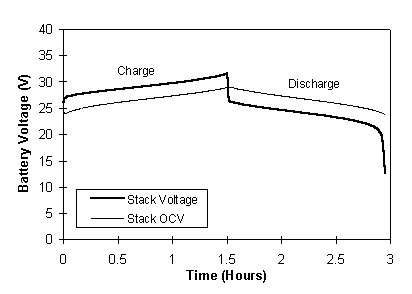
Fig. 5 Total battery voltage and open-circuit voltage
profiles at a constant charge/discharge current of 100 Amps.
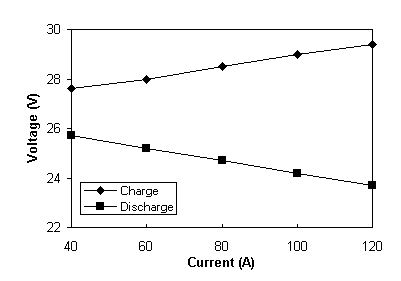
Fig. 6 Polarisation plot for the total battery system.
The average cell resistivities of the total battery system at 50% SOC
for the charge and discharge cycles were calculated as 3.66 ohms cm2 and
3.84 ohms cm2 respectively. These values compare favourably to the
theoretical values of 3.60 ohms cm2 for the charge cycle and 3.82 ohms cm2
for the discharge cycle, calculated for a parallel system from the
individual stack resistivities previously measured.
Tapping Cell Utilisation
The tapping cells are cells that allow current to be transferred into or out
of the battery in addition to the 2 end electrodes. The tapping cells were a
bipolar arrangement employing an internal copper current collector to allow
the exchange of high currents. One tapping cell was incorporated into each
stack at cell no.17. The tapping cells were also connected in the parallel
network, therefore the total battery system could be charged or discharged
across 17 or 19 cells. The main design purpose of the tapping cells was to
allow charging across 17 cells and discharging across 19 cells thus limiting
the difference between the charge and discharge voltages.
The testing of the tapping cells involved charging the battery across 17
cells at high constant currents, while ensuring that the total battery stack
voltage did not exceed 28 V. The battery was then discharged across 19 cells
until the total battery stack voltage reached 22 V.
A typical voltage profile for the 17 cells charge - 19 cells discharge, 100
A constant current cycle is illustrated in Figure 7. The upper and lower
voltage limits are also shown in the figure, highlighting the voltage limits
between which the battery was cycled.
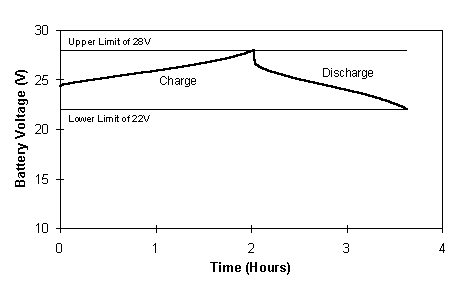
Fig. 7 Voltage profile for charge/discharge across 17/19
cells at 100A.
One of the main characteristics of this cycling which is immediately
noticeable, is the difference in length ie. time for the charge and
discharge profiles. While this would suggest a low coulombic efficiency, it
is important to keep in mind that during the charge cycle only 17 cells are
employed to charge the battery, therefore, a lower voltage is imposed. Cells
18 and 19 in each stack are at open circuit during charging, thus the charge
time utilising 17 cells will obviously be longer than when all 19 cells are
used. Similarly, it is expected that the Ahr out will be less when
discharging across 19 cells than if discharging 17 cells. However, the
voltage will be higher and within the prescribed voltage limits. Rather than
evaluating the coulombic efficiency of this battery therefore, the best
indicator of its performance is the overall energy efficiency which in this
case was up to 79%.
The results obtained at the four different currents are presented in Table
7.
Table 7 shows that at constant discharge currents below 100 A the system
meets and exceeds the 160 Ahr capacity of the nickel/cadmium system
presently employed as the back-up battery. It should be noted however, that
in the VRB battery system the capacity figures given in Table 6 are not for
a fully charged battery but for a battery that has been charged at a
constant current until the 28 V upper limit has been reached. From Figure 7
and Table 7 it is seen that approximately 2 hours are needed to charge the
battery up to 92.5 % capacity, at a constant current of 100 A. At 120 A it
only takes 1.5 hours to charge the battery up to 90.5 % capacity while not
exceeding the 28 V upper limit.
The advantage of this type of battery is immediately apparent in the
charging time required to charge the system. Ideally, a power supply system
that can handle higher currents would charge the battery in under 1 hour. It
is important to note however, that a generator works on a constant voltage
charging principle ie. as the voltage of the battery nears the upper voltage
limit set in the generator the current tapers off to trickle charging. To
gain the rapid charging benefits of the VRB system a constant current
charging supply is recommended.
Maximum Capacity Utilising Taper Charging The full capacity of the system
was demonstrated by discharging the battery from a fully charged state
(taken as 98 %).
Table 7 Results obtained at different constant currents when utilising the
tapping cells in the voltage limits of 22 V and 28 V.
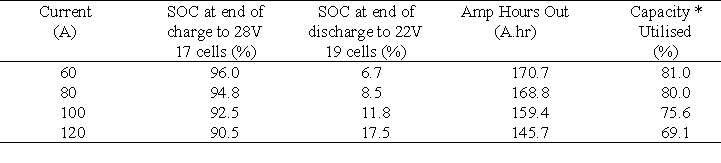
* Theoretical maximum capacity = 210.8 A.hr Based on 19 cells and 83L of
1.8M vanadium solution / half-cell.
The total battery system was charged across 17 cells at 120 A. Once the
battery was charged to the maximum SOC possible at this current, the charge
current was lowered to 100 A. This method was continued until the final
charging current reached 40 A. By this stage the battery had reached an SOC
above 98 %, the total charging time being approximately 2 hours.
The results obtained for discharging the total battery system across 19
cells at different constant discharge currents to a lower stack voltage
limit of 22 V, are summarised in Table 8 and Figure 8(a).
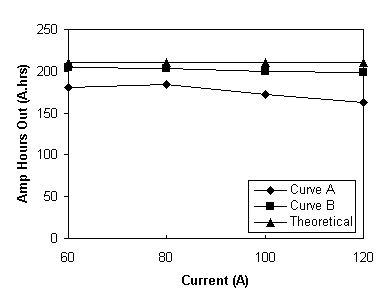
Fig. 8 Amp.hours.out versus discharge current for the
total battery system discharged from 98% SOC to a lower voltage limit of
22V. Curve (a) for a cell resistance of 3.8 ohms cm2, (b) for a cell
resistance of 2 ohms cm2.
The discharge profiles obtained are shown together in Figure 9.
At all of the currents shown in Table 8 the Ahrs out exceeded 160 Ahrs
before the battery reached the 22 V limit. The Ahrs out is a direct
consequence of how low the battery could be discharged. At 120 A the
resistance of the battery is such that when the 22 V limit is reached the
battery is only discharged to 19% SOC.
If the resistance of the battery is lower it can be discharged to a lower
state before the 22 V limit. In fact, if a cell resistance of 2.0 ohms cm2
is assumed (which is now readily achievable with available materials), at
the 22 V lower limit and 120 A discharge, the battery OCV would be 25.04 V,
this corresponding to an SOC of 17 % at the end of discharge. Similarly, at
60 A an SOC of 4 % would be reached at the end of discharge corresponding to
90 % capacity utilisation assuming similar coulombic losses as in Table 7.
The projected Amp.hours versus discharge current for a stack with a cell
resistance of 2 ohms cm2 is given in Figure 8, Curve (b)
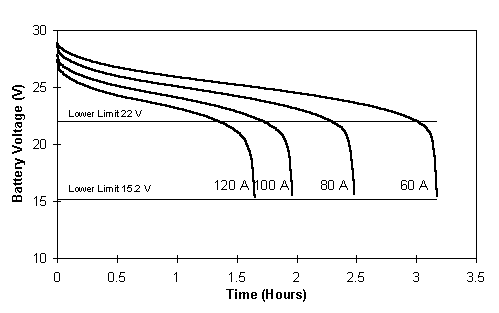
Fig. 9 Discharge voltage profiles for the fully charged
battery system showing 22V and the total discharge 15.2V limit.
A float test was carried out for over 70 hours and in that time the
total current required to keep the battery stack at the constant voltage of
26.6 V (50% SOC) was only 0.28 A.
VRB Employing Glassy Carbon Electrodes. A 19 cell battery stack was
initially constructed employing glassy carbon electrodes. The glassy carbon
material is extremely conductive and certain parts of the electrode needed
to be insulated, due to the current design of the flow-frames used for
construction of the VRB stacks. While a new flow-frame suitable for glassy
carbon electrodes is currently being designed, this was not available for
the Emergency Back-Up battery project.
Table 8 Results obtained when discharging the total battery system across 19
cells from a fully charged state to a battery lower voltage limit of 22 V.
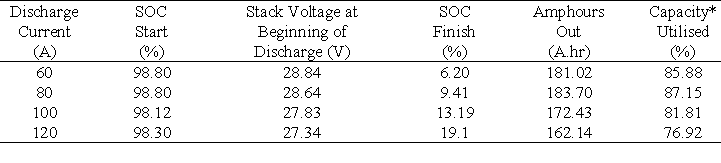
* Theoretical maximum capacity = 210.78 A.hr Based on 19 cells and 83L of
1.8M vanadium solution / half-cell.
The glassy carbon battery system was charged across 19 cells at a current of
20 A. At 85% SOC the battery charging voltage at 20 A was 28.97 V. The
voltage was also measured across 17 cells and found to be 25.89 V. The
open-circuit stack voltage across 17 and 19 cells at 17% SOC was 22.42 V and
25.06 V respectively. This again highlights the different voltages that can
be obtained at the same SOC when using the tapping cell.
The average cell resistivity calculated at 50% SOC during charging was 1.89
ohms cm2. This cell resistivity shows that low resistivities can be obtained
with currently available materials.
5. Cost Projections
The four phases of the commercialisation plan over the first six years are:
- Phase 1 - Viability Assessment
- Phase 2 - 1.5 MWh prototype
- Phase 3 - Demonstration business
- Phase 4 - Commercial Production
Table 9 projects the effect of the cost cutting initiatives and shows a plan
to reduce the cost of the cell stack components from $879 to $133 per kW.
By using economies of scale and process improvements the cost of electrolyte
is expected to be reduced as shown in Table 9.
The costs in Table 9 and 10 do not include the auxiliary systems costs
comprising of plumbing, pumps, tanks, power conversion equipment and battery
controller.
An approximate comparison of the cost per installed kW of vanadium battery
storage compared with lead acid battery for a range of hours storage is
shown in Figure 10.
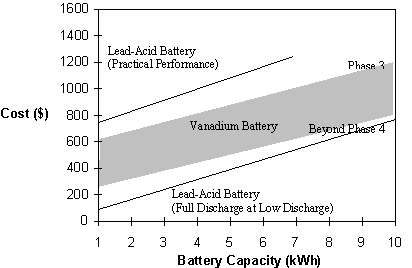
Fig. 10 Battery cost versus battery capacity.
Table 9 Cost ($/kW) of battery stack components based on a 100kW
stack.
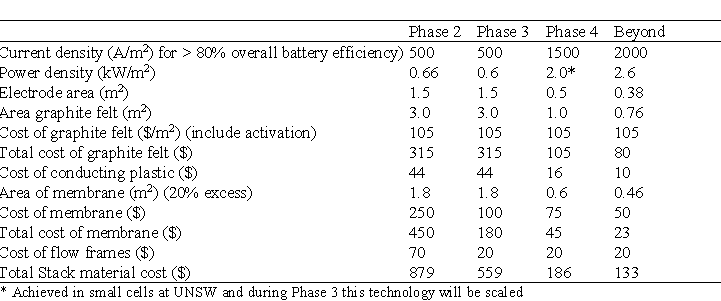
Table 10 Electrolyte Cost ($/kWh)

The total vanadium battery costs in $/kWh decrease with increasing storage
time as shown in Figure 11.
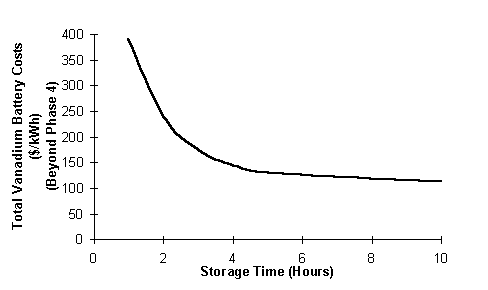
Fig. 11 Total vanadium battery costs versus storage
time.
6. Commercial Developments
To date, two commercial licenses have been granted by Unisearch Ltd for the
commercialisation of the vanadium redox battery in stationary energy storage
applications. Thai Gypsum Products (Thailand) have been granted a license to
manufacture and use the vanadium redox battery in residential photovoltaic
applications and non-grid interactive commercial peak-shaving systems in
South-East Asia. A consortium comprising Mitsubishi Petrochemicals and
Kashima Kita Power Corporation of Japan has also been licensed to further
develop and commercialise the vanadium redox battery world-wide (excluding
South-East Asia, China and Australia) in large-scale load-levelling systems.
A 200kW/800kWh vanadium battery system was commissioned in Japan in 1997 and
is currently undergoing grid-connected testing. A 2MW demonstration load-levelling
system is to be commissioned in the Tokyo area by the end of 1999.
In May 1997, Unisearch Ltd granted an option for exclusive world-wide rights
to the VRB technology for electric vehicle applications to the Australian
Company Pinnacle Mining NL.
7. Conclusion
The design and evaluation of the vanadium emergency back-up battery system
has confirmed that it has highly desirable characteristics for emergency
back-up applications. It offers many advantages over conventional type
battery systems which have restricted the design of efficient and reliable
back-up power systems.
The ability of the vanadium battery to be both mechanically and electrically
recharged provides added flexibility, as does the ability to accurately
determine the state-of-charge and capacity of the battery directly from the
open-circuit voltage of the electrolytes.
The vanadium battery system is a reliable and cost effective energy storage
system which offers independent power and capacity ratings at high
efficiencies. System design advances and energy density increases are
continuing as the system approaches commercialisation.
8. References
[1] M. Skyllas-Kazacos and R. G. Robbins, “The All Vanadium Redox
Battery”, U. S. Patent No. 849 094 (1986)
[2] E. Sum and M. Skyllas-Kazacos, Journal of Power Sources, 15 (1985) 179.
[3] E. Sum, M. Rychcik and M. Skyllas-Kazacos, Journal of Power Sources, 16
(1985) 85.
[4] C. Menictas, D.R. Hong, M. Kazacos and M. Skyllas-Kazacos, “Vanadium
Battery Solar Demonstration House”, Proceedings of the Solar `94
Conference, Sydney, Australia, Vol 2 (1994) 611.
[5] C. Menictas, D. R. Hong, Z. H. Yan, J. Wilson, M. Kazacos and M.
Skyllas-Kazacos, “Status of the Vanadium Redox Battery Development
Program”, Proceedings of the Electrical Engineering Congress, Sydney,
Australia, Vol 1 (1994) 299.
[6] C. Menictas, T. Tran and M. Skyllas-Kazacos, “The Dissolution of V2O5
in Vanadium Sulphate Solution”, Proceedings of the Ninth Australasian
Electrochemistry Conference, Wollongong, Australia, Vol 2 (194) 66.
[7] The Vanadium Redox Battery Website, “www.ceic.unsw.edu.au/centers/vrb/webframe/
option1.htm”.(1996).
[8] M. Bartolozzi, Journal of Power Sources, 27 (1989) 219.