Make your own
biodiesel
Anybody
can make biodiesel. It's easy, you can make it in your kitchen -- and it's
BETTER than the petro-diesel fuel the big oil companies sell you. Your
diesel motor will run better and last longer on your home-made fuel, and
it's much cleaner -- better for the environment and better for health. If
you make it from used cooking oil it's not only cheap but you'll be
recycling a troublesome waste product. Best of all is the GREAT feeling of
freedom, independence and empowerment it will give you. Here's how to do it
-- everything you need to know.
Three
choices
1. Mixing it
2. Straight vegetable oil
3. Biodiesel
Biodiesel
Where do I start?
What's next?
The process
Our first biodiesel
Biodiesel from new oil
Biodiesel from waste oil
Removing the water
Washing
Using biodiesel
Safety
How much methanol?
Ethyl esters -- making ethanol biodiesel
Reclaiming excess methanol
More about lye
How much lye to use?
Basic titration
Better titration
Accurate measurements
pH meters
Phenolphthalein
pH meters vs phenolphthalein
High FFA levels
Deacidifying WVO
No titration?
The basic lye quantity -- 3.5 grams?
Mixing the methoxide
Test batches
Stock methoxide solution
Poor man's titration
How much glycerine? Why isn't it solid?
PET bottle mixers
Viscosity testing
How the process works
What are Free Fatty Acids?
Iodine Values
-- High Iodine Values
-- Talking about the weather
Which method to use?
Why can't I start with the Foolproof method?
Quality
Quality testing
Cetane Numbers
National standards for biodiesel
--
standards and the homebrewer
-- standard testing
Biodiesel in gasoline engines
Home heating
Lamps and stoves
Other uses
Identifying plastics
Three choices
There are at least three ways
to run a diesel engine on bio-power, using vegetable oils, animal fats or
both. All three work with both fresh and used oils.
- Use the oil just as it is
-- usually called SVO fuel (straight vegetable oil);
- Mix it with kerosene
(paraffin) or diesel fuel, or with biodiesel;
- Convert it to biodiesel.
The first two methods sound
easiest, but, as so often in life, it's not quite that simple.
1. Mixing it
If you're mixing SVO with
petroleum diesel or kerosene you're still using fossil-fuel -- cleaner than
most, but still not clean enough, many would say. Still, for every gallon of
vegetable oil you use, that's one gallon of fossil-fuel saved, and that much
less carbon in the atmosphere.
People use various mixes, 30% petro-diesel and 70% vegetable oil, or a 50/50
mix. Some people just use it that way, start up and go, others say it needs
at least pre-heating and probably a two-tank system too, like SVO (see
below), and we agree with that. The same goes for mixes with vegetable oil
and biodiesel. In both cases, you might get away with just using it as-is
with an older Mercedes 5-cylinder IDI diesel, which is a very tough and
tolerant motor -- it might not like it but you probably won't kill it.
Otherwise, it's not wise.
To be safe, you're going to need what amounts to an SVO system with fuel
pre-heating anyway. You'll use much less petro-diesel or biodiesel by using
it in the second tank for start-ups and stops rather than mixing it 50/50.
(See next.) Or just use 100% biodiesel and don't bother with extra tanks and
pre-heating the fuel. (See after next.)
Mixes are a poor compromise. But they do have advantages in cold weather.
Some kerosene or #1 diesel mixed with biodiesel lowers the temperature at
which it starts to gel, and a mix with biodiesel will do the same for an SVO
system.
Message to the
Biofuel mailing list:
"I stuck 3 litres of pure rapeseed oil from my local supermarket straight
into the tank of my 1998 VW Caddy van. There were about 3-4 litres of
dino-diesel in the tank. Once the dino had cleared the fuel lines, I was
running on about 50% dino to 50% oil. The only differences I noticed were:
A) the engine ran about 10 deg C cooler; B) the exhaust smelt like a
roadside burger bar. Apart from that, no problems! As the weather is finally
starting to warm up here, I may increase the oil/diesel ratio and see that
happens. -- Nick"
Reply:
"One thing that will happen is that your cold starts will begin to
deteriorate. Then your filter will probably start plugging. Then your
injectors will likely, in time, get coked up. Then the spray pattern will be
wonky. Then you'll set the stage for ring sticking, glazing of the cylinder
walls, increased lube oil consumption and eventual engine failure -- if you
can continue to get the thing started in the morning. More than 20% or so in
the diesel is not a good plan for more than short term 'experiments'.
Unfortunately, you're not doing anything new here, Nick, and if it was as
easy as running high percentages of SVO in diesel, and being able to
maintain reliability, we'd all have gone that way long ago. Regards, Edward
Beggs, Neoteric Biofuels Inc"
A variation on this theme is adding a solvent to the veg oil to lower the
viscosity -- usually 3% white spirit (a.k.a. mineral turpentine, Stoddard
solvent, turpentine substitute). This raised a lot of interest after it was
publicized on a British TV program -- "just add a spoonful". It also raised
a lot of scepticism: "'experimental' at best" was the view of experienced
SVO users, and "steer well clear". We agree. Work on blends of SVO with
other solvents, such as butanol and ethanol, is still experimental. Go ahead
and experiment, but there are no guarantees.
2. Straight
vegetable oil
Straight vegetable oil (SVO)
systems can be a clean, effective and economical option.
Unlike biodiesel, with SVO you have to modify the engine. The best way is to
fit a full single-tank SVO system with different injectors and glowplugs,
injector pump adjustment, fuel pre-heating, temperature controls and extra
filters. With the German
Elsbett single-tank SVO system you can use petro-diesel, biodiesel or
SVO, in any combination. Just start up and go, stop and switch off, as
usual.
There are also two-tank systems which only pre-heat the oil, to make it
thinner. You have to start the engine on ordinary petroleum diesel or
biodiesel in one tank to warm it up, then switch to SVO in the other tank,
and switch back to petro- or biodiesel before you stop the engine, or you'll
coke up the engine and the injectors.
More information on straight vegetable oil systems
here.
3. Biodiesel
Biodiesel has some clear
advantages over SVO: it works in any diesel, without any conversion or
modifications to the engine or the fuel system -- just put it in and go. It
also has better cold-weather properties than SVO (but not as good as
petro-diesel -- see
Using biodiesel in winter). Unlike SVO, it's backed by
many long-term tests in many countries, including millions of miles on the
road.
Biodiesel is a clean, safe, ready-to-use, alternative fuel, whereas it's
fair to say that many SVO systems are still experimental and need further
development.
On the other hand, biodiesel can be more expensive, depending what you make
it from and whether you're comparing it with new or used oil (and where you
live). And, unlike SVO, it has to be processed -- you have to make it. But
the large and rapidly growing worldwide band of homebrewers don't seem to
mind -- they make a supply every week or once a month and soon get used to
it. Many have been doing it for years.
And anyway, you have to process SVO too, especially WVO (waste vegetable
oil, used, cooked), which many people with SVO systems use because it's
cheap or free for the taking. WVO has to be filtered and dewatered, and
probably should be deacidified.
Biodieselers say, "Well, if I'm going to have to do all that I might as well
make biodiesel instead." But SVO types scoff at that -- it's much less
processing than making biodiesel, they say. To each his own.
x |
Needs
processing |
Guaranteed trouble-free |
Engine conversion |
Cheaper
|
Biodiesel |
Yes
|
Yes
|
No
|
Sometimes
|
SVO/WVO |
Less
|
No
|
Yes
|
Usually
|
Costs and prices:
Biodieselers using waste oil feedstock say they can make biodiesel for 60
cents US per gallon or less. Most people use about 600 gallons of fuel a
year (about 10 gallons a week) -- say US$1,380 a year. An SVO system costs
from about $500 to $1,200 or more. So with an SVO system you'll be ahead in
a year, not a long time in the life of a diesel motor. But will it last as
long with SVO? Yes, if you use a good system. Recommendations, and much
more,
here.
Biodiesel
Converting the oil to
biodiesel is probably the best of the three options (or we think so anyway).
You could simply
buy your biodiesel instead. Most major European vehicle
manufacturers now provide vehicle warranties covering the use of pure
biodiesel -- though that might not be just any biodiesel. Some
insist on "RME", rapeseed methyl esters, and won't cover soy biodiesel in
the US, but this seems to be more a trade-related issue than a
quality-control one. Germany has more than 1,500 filling stations supplying
biodiesel, and it's cheaper than ordinary diesel fuel. It's widely used in
France, the world's largest producer. Virtually all fossil diesel fuel sold
in France contains between 2% and 5% biodiesel. New EU laws will soon
require this Europe-wide. Some states in the US are legislating similar
requirements. There's a growing number of US suppliers. Biodiesel is more
expensive than ordinary diesel in the US but sales are rising very fast and
prices will drop in time. In the UK biodiesel is taxed less than petrodiesel
and it's available commercially.
But there's a lot to be said for the GREAT feeling of independence you'll
get from making your own fuel (and it's more than just a feeling -- it's
real!).
If you want to make it yourself, there are
several good recipes available for making high-quality
biodiesel, and they all say what we also say: some of these chemicals are
dangerous, take full safety precautions, and if you burn/maim/blind/kill
yourself or anyone else, that will make us very sad, but not liable -- we
don't recommend anything, it's nobody's responsibility but your own.
On the other hand, a lot of people are doing it -- it's safe if you're
careful and sensible. "Sensible" also mean not over-reacting, as some people
do: "I'd like to make biodiesel but I'm frightened of all those terrible
poisons." In fact they're common enough household chemicals. Lye is sold in
supermarkets and hardware stores as a drain-cleaner, there's probably a can
of it under the sink in most households. Methanol is the main or only
ingredient in barbecue fuel or fondue fuel, sold in supermarkets and chain
stores as "stove fuel" and used at the dinner table; it's also the main
ingredient in the fuel kids use in their model aero engines. So get it in
perspective, no need to be frightened. See Safety
for further information. Learn as much as you can first --
lots of information is available. Make small
test batches before you try large batches (see also
Test-batch mini-processor). Make it with
fresh oil before you
try waste oil.
Where do I
start?
Start here: make a test batch
of biodiesel using 1 litre of fresh new oil in a blender. If you don't have
a spare blender, either get one (you can pick them up quite cheap
second-hand), or try
this. Or, better, make a simple
Test-batch mini-processor.
Go on, do it! Get some methanol, some lye and some new oil at the
supermarket and go ahead -- it's a real thrill!
Here's the recipe,
just use 1 litre of oil instead of 10 litres, and 200 ml of methanol instead
of 2 litres, with 3.5 grams of lye.
Here's how to use a blender, and
here's how to mix the sodium methoxide -- "Methoxide
the easy way" (also the safe way).
What's next?
Learn. You have some decisions
to make. It's all quite simple really, thousands of people are doing it,
very few of them are chemists or technicians, and there's nothing a layman
can't understand, and do, and do it well. But there is quite a lot to learn.
You should find everything you need to know right here. We've tried to make
it easy for you. You start off with the simplest process that has the best
chance of success and move on step by step in a logical progression, adding
more advanced features
First, here's how we started.
The process
Vegetable oils and animal fats
are triglycerides, containing glycerine. The biodiesel process turns the
oils into esters, separating out the glycerine. The glycerine sinks to the
bottom and the biodiesel floats on top and can be syphoned off.
The process is called transesterification, which substitutes alcohol for the
glycerine in a chemical reaction, using lye as a catalyst.
We use methanol to make methyl esters. We'd rather use ethanol because most
methanol comes from fossil fuels (though it can also be made from biomass,
such as wood), while ethanol is plant-based and
you can distill it yourself, but the biodiesel process is more
complicated with ethanol. (See
Ethyl esters.)
Ethanol (or ethyl alcohol, grain alcohol -- EtOH, C2H5OH) also goes by
various other well-known names, such as whisky, vodka, gin, and so on, but
methanol is a deadly poison: first it blinds you, then it kills you, and it
doesn't take very much of it. It takes a couple of hours, and if you can get
treatment fast enough you might survive. (But don't be put off -- it's easy
to do this safely. Safety is built-in to everything you'll read here.)
Methanol is also called methyl alcohol, wood alcohol, wood naphtha, wood
spirits, methyl hydrate (or "stove fuel"), carbinol, colonial spirits,
Columbian spirits, Manhattan spirits, methylol, methyl hydroxide,
hydroxymethane, monohydroxymethane, pyroxylic spirit, or MeOH (CH3OH or
CH4O) -- all the same thing. (But, confusingly, "methylcarbinol" or "methyl
carbinol" is used for both methanol and ethanol.) In the US you can usually
get it at race tracks.
Methylated spirits (denatured
alcohol) doesn't work; isopropyl alcohol (rubbing alcohol) also doesn't
work.
The lye catalyst can be either sodium hydroxide (caustic soda, NaOH) or
potassium hydroxide (KOH), which is easier to use, and it can provide a
potash fertilizer as a by-product. Sodium hydroxide is often easier to get
and it's cheaper to use. If you use potassium hydroxide, the process is the
same, but you need to use 1.4 times as much. (See
More about lye.) You can get KOH from soapmakers'
suppliers and from chemicals suppliers. Other chemicals, such as isopropyl
alcohol (isopropanol) for titration, are available from chemicals suppliers.
CAUTION:
Lye (both NaOH and KOH) is dangerous -- don't get it on your skin or in your
eyes, don't breathe any fumes, keep the whole process away from food, and
right away from children. Lye reacts with aluminum, tin and zinc. Use glass,
enamel, stainless steel or HDPE (High-Density Polyethylene) containers for
methoxide. (See
Identifying plastics.)
See also
Making lye from wood ash.
Our
first biodiesel
This was just an investigative
project for us when we made our first biodiesel more than five years ago in
Hong Kong. Most of the equipment was improvised. Apart from chemicals and
some beakers, syringes and things, the only thing we bought was a set of
scales.
We got about 60 litres of used oil (WVO --waste vegetable oil) from Lantau
Island's local McDonald's. There were four 16-litre cans of it, a mix of
used cooking oil and residual beef and chicken fats. Two of the tins were
solidified, the other two held a gloppy semi-liquid. We warmed it up a bit
on the stove (to about 50 deg C) and filtered it through a fine mesh filter,
and then again through coffee filter papers, but it was quite clean -- very
little food residue was left in the filters.
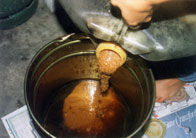
Used
cooking oil from McDonald's. |
We'd also bought 10 litres of the cheapest new cooking oil we could find --
we don't know what kind of oil it was, the tins only said "Cooking Oil" --
and used this for our first experiment.
It worked, but we've learnt a lot since then. Now it's easy to make
high-quality biodiesel every time without fail. And we don't use open
containers for processing now, and neither should you -- and mix the
methanol in closed containers too.
Practices, knowledge, technology, equipment and safety measures have all
improved tremendously in the last five years since we brewed our first
batch, thanks mainly to the collaborative work of thousands of biofuellers
worldwide at the
Biofuel mailing list and other Internet forums.
As a Biofuel list member said in 2002: "I just want to say how important
what you all are doing here is. Closed-system fuel production, on a local or
small regional scale, tied to local resources, using accessible
technologies, and dependent on entrepreneurial innovation combined with
open-source information exchange -- it's AWESOME. Keep up the good work
everyone, before the planet fries."
Biodiesel
from new oil
Make your first test-batch using new oil (fresh, virgin, uncooked). Follow
the instructions below, but use 1 litre of oil instead of 10 litres, and 200
ml of methanol instead of 2 litres, with 3.5 grams of lye. Check the quality
of your biodiesel with this basic
quality test.
We had difficulty finding pure methanol in Hong Kong, and eventually paid
the very high price of US$10 per litre for 5 litres from a wholesale
chemical supply company. It has to be 99% pure or better. (See
How much methanol?)
In the US, for small test batches, you can get DriGas from the hardware
store. One type of DriGas is methanol, another is isopropanol, make sure to
get the methanol one.
We used 2 litres of methanol to 10 litres of vegetable oil, and 3.5 grams of
pure, granular lye (sodium hydroxide) per litre of oil -- 35 grams for 10
litres. (See
More about lye.)
You can get lye at most hardware stores (Red Devil lye in the US). Shake the
container to check it hasn't absorbed moisture and coagulated into a useless
mass, and make sure to keep it airtight.
We had to be quick measuring out the 35 grams of lye required -- summer
humidity in Hong Kong is usually about 80% at 30 deg C or more, and the lye
rapidly got wet, making it less effective.
We mixed the lye with the 2 litres of methanol in a strong, heatproof glass
bottle with a narrow neck to prevent splashing. It fumed and got hot, and
took about 15 minutes to mix. See
Methoxide the easy way. (Use closed containers for
mixing methoxide.)
This mixture is sodium methoxide, an extremely powerful base which enjoys
eating stuff like human flesh -- take full safety precautions when working
with sodium methoxide, have a source of running water handy.
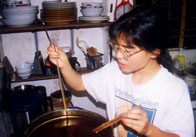
Midori checks the temperature of the oil. |
Meanwhile we'd warmed the 10 litres of new oil in a steel bucket on the
stove to about 40 deg C (104 deg F) to thin it so it mixed better. In fact,
55 deg C (131 deg F) is a better processing temperature. Don't let it get
too hot or the methanol will evaporate. (Methanol boils at 64.7 deg C, 148.5
deg F.)
We'd made a wooden jig with a portable vice clamped to it holding a power
drill fitted with a paint mixer to stir the contents of the bucket. This did
a good job without splashing.
Stirring well, we carefully added the sodium methoxide to the oil. The
reaction started immediately, the mixture rapidly separating into a clear,
golden liquid on top with the light brown glycerine settling out at the
bottom. We kept stirring for an hour, keeping the temperature constant. Then
we let it settle overnight.
The next day we syphoned off 10 litres of biodiesel, leaving two litres of
glycerine in the bottom of the bucket.
Biodiesel
from waste oil
This is more appealing than
using new oil, but it's also more difficult.
First, check for water content. Used oil often has some water in it, and it
has to be removed before processing. See Removing
the water, below.
Waste oil needs more catalyst than new oil to neutralize the Free Fatty
Acids (FFAs) formed in cooking the oil, which interfere with the
transesterification process.
You have to titrate the oil to determine the FFA content and how much lye
will be required to neutralize it. This means determining the pH -- the
acid-alkaline level (pH7 is neutral, lower values are increasingly acidic,
higher than 7 is alkaline). An electronic pH meter is best, but you can also
use pH test strips (or litmus paper), or phenolphthalein solution (from a
chemicals supplier).
We also thought of using red cabbage juice, which changes from red in a
strong acid, to pink, purple, blue, and finally green in a strong alkali
(see
Natural test papers -- Cabbage, Brazil, Dahlia,
Elderberry, Indigo, Litmus, Rose, Rhubarb, Turmeric). We didn't have a pH
meter then so we used phenolphthalein solution. Phenolphthalein is
colourless up to pH 8.3, then it turns pink (or rather magenta), and red at
pH 10.4.
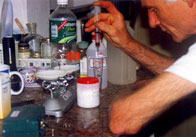
Keith
checks the pH of the waste oil. |
Dissolve 1 gm of lye in 1 litre of distilled water (0.1% w/v lye solution).
In a smaller beaker, dissolve 1 ml of the cooled oil in 10 ml of pure
isopropyl alcohol. Warm the beaker gently by standing it in some hot water,
stir until all the oil dissolves in the alcohol and turns clear. Add 2 drops
of phenolphthalein solution.
Using a graduated syringe, add 0.1% lye solution drop by drop to the
oil-alcohol-phenolphthalein solution, stirring all the time, until the
solution starts to turn pink and stays that way for 10 seconds. Take the
number of millilitres of 0.1% lye solution you used and add 3.5. This is the
number of grams of lye you'll need per litre of oil. (See
Better titration.)
Our first titration took 6 ml of 0.1% lye solution (not very good oil), so
we used 6 + 3.5 = 9.5 grams of lye per litre of oil: 95 grams for 10 litres.
Then proceed as with new oil: measure out the lye and mix it with the
methanol to make sodium methoxide -- it will get even hotter and take longer
to mix, as there's more lye this time. Make sure the lye is completely
dissolved in the methanol.
Carefully add the sodium methoxide to the warmed oil while stirring, and mix
for an hour. Settle overnight, then syphon off the biodiesel.
The first five times we did this, using 10 litres of waste oil each time, we
got biodiesel (a bit darker than the new oil product) and glycerine three
times, and twice we got
jelly. The answer is to be more careful with the
titration: do it twice, just to be sure. Read on, and you'll learn how to
make high-quality biodiesel every time, without fail.
The production rate was less than with new oil, ending with 8-9 litres of
biodiesel instead of 10. The acid-base
Foolproof method, developed since, will get much higher
production rates with heavily-used oil.
Check the quality of your biodiesel with this basic
quality test.
For a more detailed description of making biodiesel from WVO, see
Mike Pelly's method.
Removing the
water
Water in the oil will
interfere with the lye, especially if you use too much lye, and you'll end
up with jelly. Test first for water content -- heat half a litre or so of
the oil in a saucepan on the stove and monitor the temperature with a
thermometer. If there's water in it it will start to "snap, crackle and pop"
by 50 deg C (120 deg F) or less. If it's still not crackling by 60 deg C
(140 deg F) there's no need to dewater it.
See Mike Pelly's recommendations:
Removing the water.
Here's another way, from
Aleks Kac -- it uses less energy and doesn't risk
forming more Free Fatty Acids (see below) by overheating. Heat the oil to 60
deg C (140 deg F), maintain the temperature for 15 minutes and then pour the
oil into a settling tank. Let it settle for at least 24 hours. Make sure you
never empty the settling vessel more than 90%.
Here's what
Biofuel mailing list member Dale Scroggins says about
water removal:
Water in vegetable oil can
exist as free water, which will eventually settle to the bottom of a
vessel; as suspended droplets, which may settle if the oil is heated, or
the droplets are coalesced; and as water in solution with other impurities
in the oil. Free water is the easiest to remove. The droplets are removed
most efficiently by coalescing and draining. Suspended droplets that
cannot be coalesced and water in solution are more problematic.
Boiling off the water is more difficult than it appears on the surface.
Colligative properties of solutions (and some mixtures) can make removal
of the last traces of water almost impossible. Water mixed with oil will
not boil at the same temperature and pressure as pure water. As water is
removed, more heat or lower pressure will be required to remove more
water. If the oil contains salts or semi-soluble fatty acids, distillation
is even more difficult.
As the percentage of water in the solution decreases (its molar fraction)
its vapor pressure will continue to drop. Lowering pressure in the system
alone may be insufficient to sustain vaporization when the solution
becomes concentrated (the molar fraction of the solute greatly exceeds
that of the solvent). Results will vary depending upon the nature of the
water-soluble impurities in the oil. Few solutions are ideal, in terms of
Raoult's law, and in used vegetable oil, there is no way to know what
solutes are in the oil.
The important thing is how
well-used, or overused, the oil is. Titration will tell you that. The higher
the titration result, the more water it's likely to contain, and the more
difficult it will probably be to remove the water.
Start with heating to 60 deg C and settling, as Aleks Kac recommends, and if
that doesn't give satisfactory results, try boiling it off, as Mike Pelly
recommends. Then try processing small test batches of a liter or less first.
If you still have difficulties, try to find better-quality oil.
Washing
Biodiesel must be washed
before use to remove soaps, excess methanol, residual lye, free glycerine
and other contaminants. Some people (fewer and fewer of them) say washing
isn't necessary, arguing that the small amounts of contaminants cause no
engine damage.
Read what the
Fuel
Injection Equipment (FIE) Manufacturers
(Delphi, Stanadyne, Denso, Bosch) have to say about these contaminants:
Summary -- html
Full document -- Acrobat file, 104kb
See also:
Determining the Influence of Contaminants on Biodiesel Properties,
Jon H. Van Gerpen et al., Iowa State University, July 31, 1996 --
12,000-word report on contaminants and their effects. Acrobat file, 2.1Mb:
http://www.biodiesel.org/resources/reportsdatabase/reports/gen/gen014.pdf
Quality biodiesel must be washed. No, filtering it is no use, and letting it
settle for a few weeks won't help either. Anyway washing the fuel is easy,
and it's well worth the trouble.
See
Washing
Using
biodiesel
You don't have to convert the
engine to run it on biodiesel, but you do need to make some adjustments and
check a few things.
Petroleum diesel leaves a lot of dirt in the tank and the fuel system.
Biodiesel is a good solvent -- it tends to free the dirt and clean it out.
Be sure to check the fuel filters regularly at first. Start off with a new
fuel filter.
If a car has been left standing for a long time with petroleum diesel fuel
in the tank the inside of the tank may have rusted (water content is quite a
common problem with petro-diesel fuel). Biodiesel will free up the rust, and
it could clog the particle filter inside the tank. At worst the car simply
stops, starved of fuel. It's not a very common problem, but it happens.
A common warning is that biodiesel, especially 100% biodiesel, will rot any
natural or butyl rubber parts in the fuel system, whether fuel lines or
injector pump seals, and that they must first be replaced with resistant
parts made of Viton. But rubber parts in diesel engine fuel systems have
been rare or non-existent since the early 1980s -- it seldom happens, and
when it does it's not catastrophic, you have plenty of warning and it's
easily fixed. See:
Biodiesel and your vehicle -- Compatability: Rubber.
See
Biodiesel and your vehicle
Safety
Wear proper protective gloves,
apron, and eye protection and do not inhale any vapors. Methanol can cause
blindness and death, and you don't even have to drink it, it's absorbed
through the skin. Sodium hydroxide can cause severe burns and death.
Together these two chemicals form sodium methoxide. This is an extremely
caustic chemical. These are dangerous chemicals -- treat them as such!
Gloves should be chemical-proof with cuffs that can be pulled up over long
sleeves -- no shorts or sandals. Always have running water handy when
working with them. The workspace must be thoroughly ventilated. No children
or pets allowed.
Organic vapor cartridge respirators are more or less useless against
methanol vapors. Professional advice is not to use organic vapor cartridges
for longer than a few hours maximum, or not to use them at all. Only a
supplied-air system will do (SCBA -- Self-Contained Breathing Apparatus).
The best advice is not to expose yourself to the fumes in the first place.
The main danger is when the methanol is hot -- when it's cold or at "room
temperature" it fumes very little, and this is easily avoided. Don't use
"open" reactors --
biodiesel processors should be closed to the
atmosphere, with no fumes escaping. All methanol containers should be kept
tightly closed anyway to prevent water absorption from the air.
We transfer methanol from its container to the methoxide mixing container by
pumping it, with no exposure at all. This is easily arranged, and an
ordinary aquarium air-pump will do (the same one you use for washing the
biodiesel). The methoxide is mixed like this --
Methoxide the easy way, which also happens to be the
safe way. The mixture gets quite hot at first, but the container is kept
closed and no fumes escape. When mixed, the methoxide is again pumped into
the (closed) biodiesel processor with the aquarium air-pump -- there's no
exposure to fumes, and it's added slowly, which is optimal for the process
and also for safety. See
Adding the methoxide.
Once again, making biodiesel is safe if you're careful and sensible.
"Sensible" also mean not over-reacting, as some people do: "I'd like to make
biodiesel but I'm frightened of all those terrible poisons." In fact they're
common enough household chemicals. Lye is sold in supermarkets and hardware
stores as a drain-cleaner, there's probably a can of it under the sink in
most households. Methanol is the main or only ingredient in barbecue fuel or
fondue fuel, sold in supermarkets and chain stores as "stove fuel" and used
at the dinner table; it's also the main ingredient in the fuel kids use in
their model aero engines. So get it in perspective: be careful with these
chemicals -- be careful with ALL chemicals -- but there's no need to be
frightened of them.
For fire risks, see
Hazards
Next:
Make your
own biodiesel -- Page 2 |