The FOOLPROOF
way to make biodiesel
The
Foolproof Method
has been used to make many thousands of gallons of high-quality
biodiesel from all sorts of feedstock. Many individual biofuellers have
adopted it as their standard method.
In two professional biodiesel fuel analyses, two years apart,
home-brewed biodiesel made by this method met the German DIN 51606
biodiesel standards. This means the fuel is suitable for warranty repair
by VW for all their vehicles made from 1996 till today. You can make DIN
and ASTM-compliant fuel just by carefully following the instructions.
See
National standards for biodiesel
|
By Aleks Kac
Free fatty
acid to ester conversion
NOTE:
The two-stage biodiesel processes are advanced methods,
not for novices -- learn the basics thoroughly first.
The single-stage base method is the place to start.
Start here.
This is a FOOLPROOF way to
make biodiesel. No titration is required, and no extra equipment or special
equipment -- a thermometer's handy, but NO pH meter!
This is a two-stage procedure, acid first-stage, base second-stage. It is
based on the highest free fatty acid (FFA) content found in used cooking
oil, but it can be used with any waste vegetable/animal oil or fat, whether
or not it has a high FFA content. The process increases yields dramatically.
Use it as your standard method.
Introduction
To make biodiesel fuel
efficiently from used vegetable oils and animal fats we have to avoid one
major problem: soap formation. Soap is formed during base-catalyzed
transesterification (using lye) when sodium ions combine with free fatty
acids present in used (and some virgin) vegetable oils and animal fats. The
soaps diminish the yield because they bond the methyl esters to water. The
bonded esters get washed out at the washing stage but make water separation
more difficult and increase water consumption. This process takes care of
the free fatty acids.
In one early test I used a mixture of 50% heavily used cooking oil and 50%
pork lard. The result was a pure product with absolutely no trace of soap!
The biodiesel looked nice, and smelt nice, as if made from virgin oil.
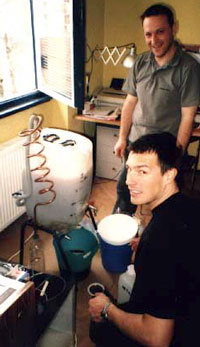
Aleks
(background) and friend Matevz making biodiesel in Matevz's living room.
|
This is a simple procedure. The first-stage process is not
transesterification, but pure and simple ESTERIFICATION. Esterification is
followed by transesterification, but under acid conditions it's much slower
than under caustic conditions and it won't do a complete oil-to-methyl ester
conversion as the reaction is much more equilibrium-sensitive. Without
methanol recovery, the alcohol overdose required would make the price of
your fuel jump, and even with recovery it would still be much more
expensive. Hence the second base-stage.
For the first stage you'll form a compound out of an acid and an alcohol.
The alcohol is still methanol, but instead of using lye (sodium hydroxide),
the CATALYST in this reaction is sulfuric acid ("battery acid"). It needs
95% sulfuric acid (battery acid is around 50%). Sulfuric acid is one of the
commonest chemicals on Earth, just like lye. More concentrated sulfuric acid
-- 98% and above -- costs more, but 95% works just fine if you follow these
directions. Other acids won't work: it must be sulfuric acid. The second
stage uses lye, as usual -- but it only uses about half as much as other
methods.
The sulfate ion in the sulfuric acid combines with the sodium ion in the lye
during the second-stage reaction to form sodium sulfate, which is a
water-soluble salt and is removed in the wash. No sulfur remains in the
biodiesel fuel product.
Equipment
You don't need a special
processor for the Foolproof method. Generally, a bottom-drained reactor
vessel is best, closed on top. Tall, narrow containers work better than
wide, shallow ones. Use a circulating pump for mixing rather than a
mechanical stirrer. The pump should take the mixture from near the bottom of
the reactor and return it via the top, to splash down on the surface. For a
35-litre reactor, a 100-W washing-machine pump will do, along with a 1.5kW
washing-machine immersion heater to heat the mixture (get a heater that's
coated with stainless steel). You could use a thermostat to control the
temperature, but they're expensive: just use a thermometer and switch on the
heater as required.
Ordinary iron and steel implements and containers will eventually corrode
because of the acid used in this process. However, you can still use the
usual 55-gal drum. The proportion of acid used in this process is very low
-- you should be able to use an uncoated drum for a year or more before the
rust gets out of control. I use a polypropylene plastic reaction vessel. Any
plastic that won't deform at 100 deg C (212 deg F) or a bit more is fine.
Stainless steel is also fine. Use an immersion heater with plastic
containers. With steel containers you can use propane heaters to heat the
oil, then switch to an immersion heater before adding the methanol.
Test batches
Whenever you're trying a new
method, it's always a good idea to make small test batches of a liter or
less first to familiarize yourself with the process before moving on to
bigger batches. Most people use kitchen blenders for this -- but don't use
it for food again afterwards!
CAUTION
Sulfuric acid is a DANGEROUS CHEMICAL. Take full safety precautions,
wear safety goggles, gloves and apron and eye protection. Have running
water nearby. Don't inhale fumes!
If you run out of sulfuric acid NEVER try to make up the required volume
with nitric acid. It may form small quantities of nitroG
(nitroglycerine) -- even the smallest amount can cause horrible
accidents. See:
High Explosives
Methanol can cause blindness and death, and it is absorbed through the
skin. Sodium hydroxide can cause severe burns and death. Together these
two chemicals form sodium methoxide. This is an extremely caustic
chemical. These are dangerous chemicals -- treat them as such! Always
have water running nearby when working with them. The workspace must be
thoroughly ventilated. No children or pets allowed. Wear safety goggles,
gloves and apron and eye protection. Do not inhale any vapors.
See
Safety for further information. |
The
process
1. Filter the used cooking oil
first as usual.
2. For a successful reaction the oil must be free of water. Here are two
methods of removing the water content:
(a) Settling the water out: This method saves energy. Heat the oil to 60 deg
C (140 deg F), maintain the temperature for 15 minutes and then pour the oil
into a settling tank. Let it settle for at least 24 hours. Make sure you
never empty the settling vessel more than 90%.
(b) Boiling the water off: Less-preferred method as it uses more energy and
helps to form more FFAs in the oil. Heat the oil to 100 deg C (212 deg F).
As the heat rises water separates out and falls to the bottom -- drain it
off to avoid steam explosions. Maintain the temperature until no more steam
bubbles rise.
First stage
3. Measure the volume of
oil/fats to be processed (preferably in liters).
4. Heat the oil to 35 deg C (95 deg F) -- make sure that all solid fats are
melted.
5. Methanol: use only 99%+ pure methanol. Measure out the methanol -- 0.08
liters of methanol for each liter of oil/fats (8% by volume). Add the
methanol to the heated oil.
6. Mix for five minutes -- the mixture will become murky because of solvent
change (methanol is a polar compound, oil is strongly non-polar; a
suspension will form).
7. For each liter of oil/fats add 1 milliliter of 95% sulfuric acid (H2SO4).
Use a graduated eyedropper, a graduated syringe or a pipette. TAKE CARE when
handling the concentrated sulfuric acid!
8. Mix gently at LOW rpm (don't splash!) while keeping the temperature at 35
deg C. The rotation of your stirrer should not exceed 500 to 600 rpm --
speed is not crucial and splashed oil is a mess to clean.
9. Maintain the temperature at 35 deg C for one hour then stop heating.
Continue stirring.
10. Stir the unheated mixture for another hour, a total of two hours, then
stop mixing. Let the mixture sit for at least eight hours, overnight is
better.
Methoxide
the easy way
Mixing lye with methanol creates an exothermic reaction, generating
heat. It's nasty stuff and it's not easy to mix -- and it must be
thoroughly mixed before you use it, with all the lye dissolved. This is
a safe and easy way to do it. The disadvantage is that you have to do it
in advance, but that's easily arranged.
Take FULL SAFETY PRECAUTIONS when working with methanol, lye and sodium
methoxide!
Use a tough, thick, container made of HDPE (High-density Polyethylene --
usually marked "HDPE" on the bottom, with the international code "2"),
with a tight stopper and a screw-on lid. Measure out the methanol into
the container. Add the required amount of lye -- if you're doing large
quantities, add it bit by bit rather than all at once, give the
container a swirl in between (replace stopper and lid first). Once it's
all added, replace the stopper and the lid, and swirl the mixture about
for a few seconds. Then let it stand. Do that a few more times, every
few hours or so (at least 4-6 times in all). It will be thoroughly
dissolved in 24 hours, or maybe a bit longer.
The proportion of lye to methanol used in making biodiesel is low,
particularly with the Foolproof method. If for some reason you're using
much higher proportions of lye, then don't do it this way.
|
11. In the meantime prepare the sodium methoxide: measure 0.12 liter of
methanol for each liter of oil/fat (12% by volume) and weigh 3.1 grams (up
to 3.5 grams if purity is in doubt) of sodium lye (sodium hydroxide, NaOH)
per liter of oil/fat. Mix the lye into the methanol until the lye is
completely dissolved.
Sodium methoxide is a DANGEROUS CHEMICAL. Take full safety precautions when
working with methanol, lye and sodium methoxide, wear safety goggles,
protective gloves and clothing, have running water nearby.
NOTE: This process uses only about half the usual amount of
lye as there is less fat left to transesterify. Use 99%+ pure sodium
hydroxide lye. After opening the container, close it again as quickly as
possible to prevent moisture getting in. Weigh the lye carefully -- using
too much will complicate the washing process later.
12. After settling for eight hours, or the next morning, pour half of the
prepared methoxide into the unheated mixture and mix for five minutes. This
will neutralize the sulfuric acid and boost the base catalysis. If you've
used solid fat, it probably solidified during settling -- gently melt the
mixture first.
Now you can continue with the normal procedure with the lye as the second
stage.
Second stage
This is the base-catalyzed
stage.
13. Heat the mixture to 55 deg C and maintain for the whole reaction.
14. Add the second half of the prepared sodium methoxide to the heated
mixture and start mixing at the same low speed of not more than 500 to 600
rpm.
TAKE CARE when handling the sodium methoxide -- full safety precautions!
15. Optional: If your reactor allows for it, start draining glycerine
by-product from the bottom 20-25 minutes after the start of the base stage.
(Pump-mixing works best for this -- with pump or mixer, turn the motor off
for a few minutes if necessary to allow the glycerine to settle.) Repeat
every 10 minutes -- take care, the glycerine is quite hot and caustic! Set
aside -- see step 18.
16. All users: Take regular samples in a 1" to 1.5" diam. glass container.
Watch for a straw yellow color of the ester portion. Glycerine (brown and
sticky) will settle at the bottom of the jar. When this color is reached
(usually in 1.5-2.5 hours) turn the heat and mixer off. Instead of taking
out samples to check the color you could use translucent braided tubing for
the pump.
17. Allow to settle for one hour.
18. Optional: For easier washing: Drain off the glycerine. Measure off 25%
of the total glycerine (including previously drained glycerine if you
followed step 15) and mix with 10 milliliters of 10% phosphoric acid (H3PO4)
for each litre of oil/fat processed. The mixing can be done with a wooden
spoon in a plastic container. Pour the acidified glycerine back into the
reactor and stir for 20 minutes, unheated. Allow to settle for at least six
hours and then drain the glycerine fraction completely.
THIS IS IT. During the first stage, free fatty acids were
esterified and some triglycerids were transesterified. The base-catalyzed
stage does only transesterification, but it's much quicker and more
complete.
Washing
19. Use the bubblewash method,
but no need to monitor pH anymore. Just add a little 10% phosphoric acid
(H3PO4) to the washing water first, 10 millilitres per gallon, just to be on
the safe side -- I don't want ANY lye floating around my fuel pump.
If you are curious about the results of your wash, use ordinary litmus
paper, it will tell you the rough pH level (acidity/alkalinity). The end
result should be neutral (pH7) or just below neutral.
20. Use one-third the volume of water as the amount of biodiesel to be
washed. Make sure both the water and biodiesel are roughly the same (room)
temperature. Pour your biodiesel into the vessel with the water, throw in
the aquarium stone and start the air pump. Let it bubble for 24 hours
minimum. Turn the pump off and let the mixture settle for half an hour. The
water will fall to the bottom, turning completely white, and the fuel you
made will be much lighter in color now. Drain the water, repeat the
procedure two more times. Remove the biodiesel from the vessel, taking care
not to get any water with it. (See also
Washing.)
21. Let the biodiesel stand for about three weeks and use only when it
becomes crystal clear; take a sample in a large marmalade jar and wait until
it is completely cleared. Put it on your window shelf and enjoy looking at
it while it clarifies. (If you want quicker results, heat the biodiesel to
45 deg C, 113 deg F, and let it cool.)
NOTE: A deposit may form in the bottom during settling --
don't let it get in your fuel tank!
Acid-stage
questions
A question will probably
arise: why not mix the methanol with the sulfuric acid before adding them to
the oil/fats? Two major reasons: (a) the reaction between methanol and
concentrated H2SO4 is quite violent and it could splash, which doesn't
happen if you mix it as described; and (b) dimethyl ether can form. Mixing
alcohols with concentrated H2SO4 is a way to dry the alcohols (which is
good) and also a way to make di-alcohol ethers, not good: dimethyl ether is
a gas, colorless and highly explosive.
Base-stage
questions
The second-stage product
should be quite murky. This is no problem, as it will wash out.
After the processed oil/fat has turned straw-yellow (step 16), you've let it
settle for an hour and drained the glycerine, you should have a total of
about 120 ml of glycerine per litre of oil/fat used. If it's less than about
100 ml/litre oil, something's wrong, even if the color is right -- the
process hasn't gone far enough.
This will almost certainly be due to carbonated lye. Lye has a really
limited shelf life: CO2 from the air neutralizes it and forms sodium
carbonate. Carbonated lye is much whiter than pure lye, which is almost
translucent. The carbonate in the lye won't harm the reaction, but you'll
have to use more lye.
The solution: Repeat the procedure from step 13. Prepare a fresh batch of
methoxide with 0.03 liters of methanol and 0.75 grams of lye for each liter
of oil/fat. Reheat the biodiesel to 55 deg C, add the fresh methoxide and
mix as before. No need this time to remove glycerine during the processing
as in step 15, and don't worry about the color. Mix for one hour, settle,
drain off the extra glycerine, and proceed from step 18.
If you plan to continue using the carbonated lye, make sure to increase the
amount by 25% next time you make biodiesel. Store lye at room temperature,
in dry conditions if possible, with the container lid really tightly closed.
Methanol
recovery (optional)
To keep costs down, even
amateur biodiesel producers try to salvage the unreacted methanol. There are
two major methods to do this: heat extraction and vacuum/heat extraction.
Heat extraction
Heat the second-stage product to 70 deg C in a sealed boiler/vessel and lead
the fumes into a condenser. Intercept the condensed methanol in a liquid
trap. Take great care because methanol is highly flammable and the fumes are
explosive. The temperature will need to be increased as the amount of
unreacted methanol in the mixture decreases.
Vacuum/heat extraction
This is basically the same as heat extraction, but it requires less energy.
The drawback of this method is that you need a special vessel and equipment
to do this. A good example is Dale Scroggins's reactor:
http://home.swbell.net/scrof/Biod_Proc.html
When building your reactor it may be a good idea to take one step at a time.
Build the reactor, get confident with the process and eventually upgrade to
methanol recovery.
At least a quarter of the methanol used can be recovered -- ie, 50+ ml per
litre of oil/fat. Mix it with fresh methanol for preparing the next batch of
methoxide.
Quality
Diesel engines require quality
fuel. You just can't pour poor-quality biodiesel into the tank and expect
the engine to go on and on without problems. You have three very dangerous
enemies: free glycerine, poorly converted oils/fats and lye. Free glycerine
and mono-, di- and triglycerids (poor ester conversion) will form gum-like
deposits around injector tips and valve heads, lye can damage the injector
pump. The key to good fuel is to just do it right and finish it! Use pure
chemicals (sulfuric acid, sodium lye and methanol) and measure them
accurately, and follow the instructions carefully -- this will take care of
poor conversion. Proper washing will get rid of the glycerine and neutralize
any remaining lye.
There are also kits available for various quality tests. I was told in a
letter from one of the visitors to our site of a test used by the motor
industry for determination of glycol in motor oil. This should work for free
glycerine determination.
"For glycerine analysis I suggest that you get a test kit for determining
ethylene glycol in motor oil. This test is simple and it generates a purple
colour if substantial free glycerol is present. Just analyze the biodiesel
as if it were motor oil. Used-car dealers use the test to determine if there
are leaks in the cooling system. Glycol and glycerol give the same result in
the test." (With thanks to Martin Reaney)
Paper chromatography and thin layer chromatography will tell you the
conversion rate, and titration may tell you about any remaining lye.
(See also
Biodiesel and your vehicle.)
Aleks Kac
Ljubljana
Slovenija
© Copyright Aleksander
Kac, 2001. Patents pending. This is a proprietory process. This
material may be copied and distributed for non-commercial education purposes
only, as long as the source of the material is stated and a reference to
this website URL is included:
http://journeytoforever.org/biodiesel_aleksnew.html
Anyone may use this process to produce fuel for their own use or for
non-commercial or educational purposes. Commercial use of the process
requires a licence from the patent holders.
Biofuels at
Journey to Forever
Biofuel
En español --
Biocombustibles, biodiesel
Biofuels Library
Biofuels supplies
and suppliers
Biodiesel
Make your own
biodiesel
Mike Pelly's
recipe
Two-stage
biodiesel process
FOOLPROOF biodiesel process
Biodiesel
processors
Biodiesel in Hong
Kong
Nitrogen Oxide
emissions
Glycerine
Biodiesel
resources on the Web
Do diesels have
a future?
Vegetable oil
yields and characteristics
Washing
Biodiesel and
your vehicle
Food or fuel?
Straight vegetable
oil as diesel fuel
Ethanol
Ethanol resources on
the Web
Is ethanol
energy-efficient? |