No - not real gold,
and not fool’s gold either - but rather a whole lot of potential
value. Them Thar Waste Hills consist of large piles of municipal
solid wastes; culm, gob, and waste coal piles; phosphogypsum
stacks; and overburden piles from oil sands strip and pit mining.
The waste hills range in size from a small to large. The very
small hill, for example, of municipal solid wastes (MSW) at
beautiful Key West, Florida is also the highest point in the city
unless the two latest hurricanes have dispersed the wastes to the
adjacent ocean. Other MSW hills are many times larger.
The potential value associated with all such waste hills
depends entirely on how they are managed.
Traditional MSW management for the last 75 years called for
burying the wastes and covering them with dirt until the landfill
site could hold no more, eventually forming a large hill at full
capacity. Some 25 years ago enterprising waste-to-energy companies
started a new management approach by generating electricity from
MSW. This was accomplished by burning the MSW to create heat. The
heat was used to produce high pressure steam. The steam in turn
powered a steam turbine electric generator. The resulting
waste-to-energy plants are commonly referred to as mass burn MSW
waste-to-energy facilities.
During the last 15 years marketplace efforts have been made to
prevent the continuing discharge of methane gas from landfills.
Methane gas is the most detrimental greenhouse gas, perhaps 20
times as harmful to the environment as carbon dioxide gas. By
burning the methane in a gas powered electric generator the gas is
converted into carbon dioxide gas as electricity is produced.
Next generation waste management may be significantly improved
by using different technology to better manage solid wastes. The
next generation technology calls for the anaerobic digestion of
MSW that produces biogas in the same manner that landfills produce
biogas. Municipalities are quite familiar with anaerobic digestion
technology since some 10,000 already own and operate anaerobic
digesters and have been doing so for the last 75 years. The biogas
can be beneficially used by generating electricity in the same
manner that landfills are converting methane gas to electricity.
This method of waste management, however, is easily capable of
producing over twice as much electricity as mass burn MSW
facilities are able to accomplish by using improved anaerobic
digestion technology.
There are now over 100 MSW-to-energy plants in operation in 31
states throughout the United States. These plants incinerate about
15% of the total trash generated or about 105,000 tons per day. On
a consolidated basis, these plants generate approximately 2,769
megawatts of electricity. The investment in capital facilities
totals more than $10 billion. These MSW-to-energy (also called
biomass-to-energy) plants represent extremely inefficient
conversion of Btus (British Thermal Units) to electricity. The
total electricity generated can be converted into equivalent Btus
by multiplying the total kWh by 3,414. 2,769MW x 1000 kW/MW x 24h
x 3,414Btu/kWh = 226,880,784,000 Btus. The total 105,000 tons of
trash per day is equivalent to 105,000 x 2,000 lbs/ton =
210,000,000 lbs/day. Dividing the total Btus/day by the lbs of
trash/day results in an average Btu/lb of trash or 226,880,784,000
divided by 210,000,000 = 1,080 Btu/lb average. Since MSW has a
rather well known Btu value of about 4,750 Btu/lb, the total
system conversion efficiency of existing MSW-to-energy is 1,080
divided by 4,750 x 100% = 22.7%. According to the US Department of
Energy, biomass-to-electricity through pyrolysis technology (same
as mass burn MSW facilities) exhibits an efficiency of
approximately 20%. These dismal efficiencies of dry processing
are, for the most part, attributable to the inherent high moisture
content of biomass.
Anaerobic digestion technology is a wet rather than dry
process. Moisture is a process requirement rather than an
operational detriment. The ability of anaerobic digestion to
convert Btus into electricity may be theoretically determined as
follows: MSW has an average organic content of about 70%. 70% of
210,000,000 lbs/day = 147,000,000 lbs/day. Of this amount,
approximately 75% are volatile solids or 0.75 x 147,000,000 =
110,250,000 lbs/day. The new and improved OAT(™) process of
anaerobic digestion produces about 12 cubic feet of methane/lb
volatile solids. The total methane produced at 99% volatile solids
to methane efficiency is found by 110,250,000 x 12 x 0.99 =
1,309,770,000 cubic feet/day.
The next step is to convert the methane into electricity. The
hourly methane production is found by dividing the daily
production by 24 or 1,323,000,000/24 = 54,573,750 CFH (cubic feet
per hour). This figure divided by about 12 equals the kW sized gas
generator that would convert the total methane into electricity or
54,573,750/12 = 4,548,000 kW. kW/1000 = MW or 4,548,000/1000 =
4,548 MW or 1.64 times as much as existing MSW-to-energy mass burn
technology. This establishes a greatly improved
biomass-to-electricity efficiency to 36%. By adding combined cycle
generation, the efficiency increases above 50% or more than twice
as much electricity than existing state-of-the-art mass burn MSW
facilities. Combined cycle refers to the practice of using the
waste heat from a power generation device to produce steam. The
steam, in turn, is beneficially used to produce additional
electricity through the use of a steam turbine generator. Steam
generation is the only method of making electricity in existing
mass burn MSW facilities. The splendid improvements in generation
efficiency can be accomplished by applying common scientific
principles to existing and fully established well known
technologies. New technology doesn’t have to be created. Existing
technologies must be used in a different manner than before. It’s
that simple.
The use of new and improved anaerobic digestion technology to
manage MSW is therefore far more effective than existing waste
management practices in terms of total marketplace value produced.
A bit of gold from a pile of trash one might conclude.
Coal provides nearly 50% of the electrical generating fuel in
the United States and similar percentages apply around the world.
Coal is more abundant than oil, if fact, coal reserves are far
more abundant than oil reserves. There is enough coal on the earth
to supply all the current energy requirements of the entire planet
for hundreds of years. Coal is many times more abundant than the
reserves of all other fossil fuels combined.
In the normal mining of coal its overburden must first be
removed. The resulting piles of overburden materials become waste
coal. They are called "culm" piles in the eastern Pennsylvania
anthracite coal region and "gob" or "boney" piles in the
bitiminous coal mining regions of western Pennsylvania, West
Virginia, and elsewhere.
The Susquehanna River is the nation’s sixteenth largest river
and is the largest river lying entirely in the United States that
flows into the Atlantic Ocean. The Susquehanna and its tributaries
drain 27,510 square miles spread over parts of the states of
Maryland, New York, and Pennsylvania. The river meanders 444 miles
from its origin at Otsego Lake near Cooperstown, New York until it
empties into the Chesapeake Bay at Havre de Grace, Maryland. The
Susquehanna contributes one-half of the freshwater flow to the
Bay. Acid mine drainage occurs in several tributaries to the
Susquehanna.
Acid mine waste pollution is caused by the physical and
chemical weathering of a very common mineral. The main culprit
seems to be iron pyrite, a mineral as "fool’s gold". The level of
acidity and the concentration of heavy metal pollutants in the
mine drainage can be directly correlated to the amount of pyrite
in the area around the mine. Physical weathering of the pyrite is
essential to reduce the grain size of the mineral. The early
miners inadvertently accelerated this process by grinding up the
ore and dumping the overburden in the mine tailings piles.
Raw coal may be sold as mined or may be processed in a
beneficiation/washing plant to remove noncombustible materials (up
to 45% reduction in ash content) and inorganic sulfur (up to 25%
reduction). Coal beneficiation is achieved with wet physical
processes such as gravity separation and dissolved air flotation.
Beneficiation produces two waste streams: fine materials that are
discharged as a slurry to a tailings impoundment, and coarse
materials (typically greater than 0.5 millimeters in size).
Whether gob/culm piles or tailings ponds the chemistry of acid
mine drainage remains the same namely the chemical oxidation of
pyrite described in the following reactions:
Iron II ions and acidic hydrogen ions are released into the
waters that runoff from the mine drainage tunnels or tailings
piles. Iron II ions are oxidized to form iron III ions as shown in
the following reaction:
The iron III ions now hydrolyze in water to form iron III
hydroxide. This process releases even more hydrogen ions into the
aquatic environment and continues to reduce the pH. The iron III
hydroxide formed in this reaction is called “yellow boy”, a
yellowish-orange precipitate that turns the acidic runoff in the
streams to an orange or red color and covers the stream bed with a
slimy coating. Aquatic life that dwells on the bottom channel of
the stream is soon killed off. Equation 3 describes this reaction:
If we were to look at the net effect of equations 1-3, we would
find that the pyrite is oxidized releasing acidic hydrogen ions
into the water and coating the stream bed with "yellow boy". The
sum of equations 1-3 is shown in the following reaction:
Complex systems in nature such as mine tailings piles and mine
draining tunnels cannot be described by just a few equations.
Other chemical reactions are occurring as shown in equation 5. In
addition, sulfides of copper, zinc, cadmium, lead and arsenic will
undergo similar geochemical reactions resulting in the
contribution of toxic metal ions into mine waste water. Other
factors such as the presence of acidic tolerant bacteria (ex.
Thiobacillus ferroxidans) can also speed up the process of sulfide
oxidation.
There are thousands of gob and culm piles, tailings ponds, and
associated discharge streams that continue to inflict
environmental damage. Remediation efforts to date have consisted
of revegetation. Revegetation does little to stop acid mine
drainage damage as every rainfall event continues to add to the
acid mine drainage volume through waste coal percolation.
Nationally, waste coal has an average of 60% of the BTU value
(British Thermal Units, a unit of energy) of normal coals. It can
take up to twice as much waste coal to produce the same amount of
electricity. This means that, in most places, waste coal burners
can only be economically built where huge volumes of waste coal
exist. It would cost too much to truck far-away low-BTU fuel to a
centralized burner. Consequently, even if waste coal burning were
a clean solution, it wouldn't deal with the problem of more
isolated waste coal piles. Burning waste coal doesn't make the
waste go away. If 100 tons of waste coal are burned, 85 tons will
remain as waste coal ash.
Since far more mercury and other toxic contaminants enter a
waste coal burner to produce a given amount of electricity, these
high levels of toxic contaminants have to come out somewhere.
Toxic metals cannot be destroyed by burning them. To the extent
that they are captured in pollution controls (protecting the air),
they are then concentrated in the highly toxic ash that ultimately
threatens the groundwater wherever this ash is dumped. Waste coal
burners have cleaner air emissions than antiquated coal plants due
to their better pollution controls, but this only means that the
ash is far more toxic, since the highly toxic particulates
captured in pollution control equipment end up in the ash. The
industry claims that 99.8% of the mercury in the fuel is captured
and ends up in their ash.
Waste coal ash is dumped in communities not far from the waste
coal burners, threatening the groundwater with leaching lead,
mercury and other poisons. Power plant waste is allowed to be
dumped without the basic protections (landfill liners) that are
required for dumping household trash. When burning any solid fuel,
the resulting ash has a higher surface area than the raw, unburned
material. The dangers of toxic leaching from ash can be expected
to be greater than from the unburned waste coal. The industry
claims that by injecting limestone into the ash, the ash becomes
impervious to leaching. However, this has not been proven and it
seems likely that the alkaline affects of the lime would afford
only temporary protection, especially since the region where most
of the waste coal burners are (Pennsylvania, West Virginia)
suffers from the nation's worst acid rain that would tend to
deplete the effects of lime addition.
The waste coal burning industry's own data shows that waste
coal ash does in fact leach metals into groundwater, despite their
public assertions to the contrary. Ashes at 2 of 12 facilities
studied in Pennsylvania were shown to contain levels of arsenic
higher than the maximum allowable concentration set forth for land
application of sewage sludge. Of 221 samples of leachate from
waste coal ash at the ash dumps, lead contamination in 23 samples
(10.4%) exceeded a level 10 times higher than EPA's maximum
contaminant level (MCL) for drinking water. Six samples exceeded
this "10 times the drinking water standard" level for cadmium, as
did single samples for chromium and selenium. In short, the
chemistry of acid mine drainage from gob/culm piles and tailings
ponds remains the same for waste coal ash.
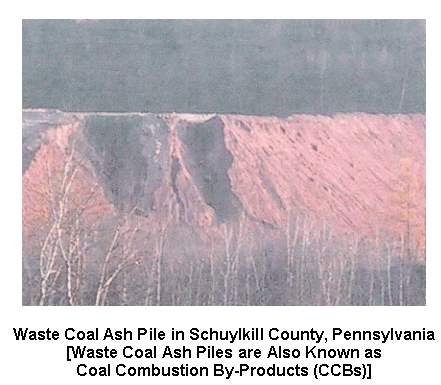
To join in on the conversation or to subscribe or visit
this site go to: http://www.energypulse.net
Copyright 2005 CyberTech, Inc.
|