by William E. Moore and Timothy J. Rittof
Waste systems of an electric power generating station are
surprisingly challenging to both chemists and chemical engineers. That
challenge is a two-part one: 1) Water must be made available for the
various station uses and be of appropriate quality and, 2) the resulting
wastewater streams must be handled in an appropriate manner. That manner
is frequently zero liquid discharge (ZLD).
The station’s water uses have capacity demands that vary from a few
hundred gpd (potable water) to thousands of gpm (cooling tower makeup);
and purity requirements that vary from a few ppb (injection water) to
over a thousand ppm (again, cooling tower makeup).
Variability of resulting wastewaters is no less daunting. Polishing
demineralizer regeneration waste is, arguably, the easiest - leave it
for the service DI supplier. Flue gas desulfurization (FGD) blowdown is
the most difficult - high chloride, high dissolved solids and saturated
with calcium. In this article, we’ll leave FGD blowdown alone and deal
with the most common problem - cooling tower blowdown (CTBD).
• Simple Cycle: A simple cycle system is an engine
directly connected to a generator with no heat recovery. The lowest
volumetric demand for water comes from the simplest of the engine-driven
generating installations. If the engine is a piston engine, the only
requirement is for cooling of the lubrication oil. The gas turbine
engine adds the use of water for inlet gas cooling and for NOx
suppression.
All installations have a demand for both potable and process water.
Depending on availability of “city water,” only one supply may be
needed. Likewise, depending on permit requirements and the availability
of “city sewer,” discharge treatment may be limited to an oil separator.
Although the volumetric demand of the simple-cycle is low, the
requirement for process water quality is not. A quality standard for the
water used in the gas turbines is specified by the supplier and is more
stringent than most steam turbine specifications and all boiler
specifications.
• Combined Cycle: The addition of a heat recovery steam
generator (HRSG) and steam turbine to the gas turbine exhaust brings us
the combined cycle generating station.
This change doesn’t increase the stringency of the required water
quality but it does change the required water volume. The steam turbine
requires a heat sink - a condenser and cooling tower.
• Coal-fired: At their simplest, the water quality
demands of the coal-fired power plant are often less stringent than
those of the gas-fired turbine plant. But, they’re more varied and
substantially larger. The coal-fired plant has coal transport, ash
disposal, fly ash collection and fly ash disposal and flue gas
desulphurization to consider.
If we lump these additional considerations under “Service Water,” the
water flow diagram for the coal-fired plant (see
Figure 1) is very close to that
of the combined cycle gas turbine plant.
The combined cycle gas-fired turbine generating plants are
significantly more efficient in converting heat to electricity than
their fired boiler siblings. This translates into less wasted heat and
less water evaporation to carry the waste heat away. Table 1 shows a
comparison of the water demands of the conventional thermal-based power
generation schemes. Coal requires twice the water of combined cycle gas
turbine.
Simple values like gallons per kilowatt-hour (gal/kWh) are very
useful for comparisons but not for design. A real operating evaluation
is much more complex. Operation throughout the year must respond to
ambient temperature, humidity, regional power demand, and power selling
price. The station operator will adjust the amount of inlet air cooling
and cooling tower blowdown; the amount of power augmentation; maybe even
duct firing. Depending on the particular situation we pick, the water
demand can be as low as 0.15 gal/kWh or as high as 0.37 gal/kWh. A coal
plant has a similar range - just twice as large. So, we have our first
water system design choices: how much water and wastewater storage and
how much wastewater processing capability. If the station is not ZLD,
selecting how big the wastewater pipe will be is a fairly simple matter.
In general, any ZLD design capacity above the requirement of “station
design” should be carefully (re)considered. The higher demand cases
rarely (if ever) last more than 16 hours out of 24 and this can readily
be covered by tankage. Tanks are cheaper than processing equipment.
Now that we have the water demand in hand, we face the interesting
task of finding a source and deciding what to do with it. We may use
surface, well or reclaim water. We may have reclaim water meeting
California Title 22 standards or we may have an industrial water meeting
no known standards. We may have only brackish water or seawater. The
sequence we suggest to examine the water character and to determine
water treatment is: 1) suspended matter, 2) chemical composition, and 3)
organic matter.
Suspended matter is chosen first because it’s the most clear. The
suspended solids concentration in the cooling tower needs to be limited
- usually to less than 100 mg/L. If the supply water contributes more
than this, clarification or filtration (or both) - either supply or side
stream - is needed. The portion of the water supply sent to the boiler
makeup water demineralizer always needs filtration.
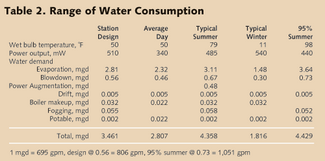
|
Chemical composition is the fun part - at least for a water chemist.
It would be nice to have a simple, clear method to analyze and to
present the character of water chemistry and implications for treatment.
In the mean time, there’s a choice of pictorial representations and
diagrams: Ternary, Jäneke, Piper, Durov, Stiff, Schoeller. We usually
choose to use two plots that everyone can prepare and seem to fit our
needs quite well: the radial (or radar) diagram and the Schoeller
diagram. The radial diagram presents the relative contribution of the
major constituents reported as calcium carbonate or as “equivalents.”
This a modification of the Stiff diagram and is readily presented from
spreadsheet software. Unfortunately, the radial diagram doesn’t
represent the total concentration of dissolved matter. For that, we use
the Schoeller chart, which is a category plot of the log of the
equivalent concentration for the major constituents. Again, the charts
are easily prepared by spreadsheet software. Examples of the radial
diagram and Schoeller charts are shown in Figure 2.
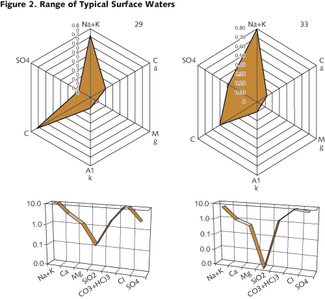
|
Conclusion
In Part II of this article, we’ll just discuss the major constituents.
At some time (preferably before commissioning) all of the bad actors -
scale formers, concrete and metal corrosive agents, and biological food
sources - must be considered.
About the Authors: William E. Moore is a senior water treatment
specialist at Calpine Corp. of Houston, TX. Timothy J. Rittof is a
senior technical fellow at HPD, a Veolia Water Solutions & Technologies
company based in Plainfield, IL, that manufactures crystallization,
evaporation, distillation and membrane separation systems. This two-part
series is based on a paper presented at the 66th International Water
Conference in Orlando, FL, in October 2005. Contact: 800-927-0319 or
timothy.rittof@veoliawater.com
Industrial WaterWorld March, 2007
Author(s) : William Moore
Timothy Rittof
Interested in a subscription to Industrial
WaterWorld Magazine?
Click here to subscribe!
This article originally published at:
http://ww.pennnet.com/display_article/289976/64/ARTCL/none/none/ZLD-Today,-Part-1--Matching-Water-Treatment-Options-to-Power-Plant-Requirements/?pc=ENL
where enlarged photos are available.
|