René Umlauft, CEO of Siemens' Renewable Energy Division, says the share of renewables will certainly increase: “Today we are talking about – world wide – 3% renewable energy consumption. That will grow to 17% by 2030. We need a good mix of energy.”
Dr Bernd Utz, Head of the Project Desertec Initiative at Siemens, says that CSP works best in areas with direct insolation (as opposed to solar photovoltaics, or PV) which can operate in diffuse sunlight). CSP can also operate with much higher ambient temperatures than PV without losing efficiency.
The company uses parabolic trough CSP technology believing it to be the most advanced and the most bankable. This technology reflects the sun's rays onto a receiver tube filled with synthetic thermal oil. The heated oil is brought to a heat exchanger where the thermal power is transferred to water, which is then used to run a steam turbine producing electricity.
Despite relying on steam, CSP plants do not use large amounts of water. Water is used for cleaning the mirrors and if the plant is water cooled some water will be used by the cooling towers. In regions with a scarce water supply, air cooling is normally used although it is less efficient than water.
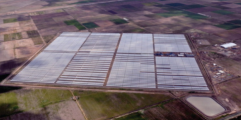
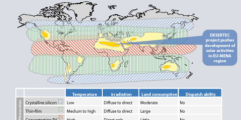
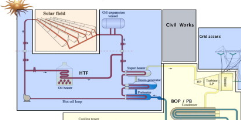
Modified steam turbines
The steam temperatures achieved with CSP [370-550°C] are much lower than in regular steam-powered plants. The quick start-up times in a CSP plant also require special turbines, as conventional steam turbines need hours to reach their optimum working speed. Umlauft says the aim is to get to a start-up time of less than 20 minutes for CSP steam turbines.
Siemens has an 80% market share for power plant steam turbines, including CSP plants. The company has adapted its SST-700 DRH two-cylinder reheat industrial steam turbine for CSP with power ratings of up to 175 MW. This has a special casing which protects the turbine from cooling down too much at night, and the low weight of the rotor enables it to start quickly, which is crucial for an efficient CSP plant.
Siemens manufactures steam turbines for all types of CSP technology other than Sterling dish engines – i.e. parabolic trough, linear Fresnel and solar tower power plants. The company also manufactures turbines for joining combined cycle and solar thermal power plants.
With its acquisition of Israeli business Solel last autumn, Siemens says it can now provide 70% of a CSP plant's parts including components, solar field and power block. Solel's technology uses synthetic thermal oil as the heat transfer fluid (HTF).
“No one else in the world has such a portfolio of concentrated solar power,” says Umlauft. “Our portfolio is the most developed.”
Siemens is also looking into alternatives for CSP HTFs. In March 2009, it acquired a 28% share in Archimede Solar Energy, an Italian company that produces receiver tubes using liquid salt instead of synthetic oil.
Heat transfer fluids – which is the best? |
OilOil has the advantage of being a proven technology as it has been used in CSP technology for over 20 years. However, it can only operate at temperatures up to 400°C, which affects the efficiency of the steam cycle. Oil is flammable and toxic, and if the CSP plant uses storage, there are three heat exchange cycles – oil, steam and storage – which decreases efficiency further. Molten saltMolten salt is stable at temperatures up to 550°C, which increases overall efficiency of the power plant. It is also easy to integrate with storage (molten salt storage). However, salt freezes when temperatures drop towards 100°C, so it needs to be kept warm over night, which uses power. WaterWater is simple in the sense that it works well and can be used directly in the steam cycle, but its usefulness is still under discussion and it is not yet a proven HTF. |
The advantages of liquid salt are that, unlike oil, the salt does not need replacing over time and works at temperatures of up to 550°C – allowing the steam turbine to operate at greater efficiency. Synthetic thermo oil, on the other hand, cannot withstand temperatures above 400°C. Liquid salts can also store heat.
Receiving the sun
The receivers are a major part of a CSP plant as they heat the HTF before reaching the steam turbine. CSP receivers have already seen a 50% increase in efficiency compared to 20 years ago. Umlauft says Siemens intends to optimise this further through higher absorption by, for example, making the receiver longer and thicker.
Siemens' UVAC 2010 solar receivers consist of a stainless steel tube enclosed in a glass cylinder with a vacuum between the steel tube and cylinder. Utz says the receivers have a heat loss of less than 9% when using oil as HTF.
When asked to compare the UVAC receiver with receivers from competitors such as SCHOTT Solar, Utz says the company does not wish to compare Siemens' technology with that of its competitors. He does reveal, however, that they differ in both “construction and performance”.
The market
In 2009, Siemens' Renewable Energy Division had revenues of €2.9 billion, €4.8bn in new orders and a profit of €0.4bn. At the moment, the world's renewable energy market is estimated to be €8.7bn, something that could increase to €270bn by 2020. According to Umlauft, solar PV will have a 36% share of this and CSP an 8% share.
Umlauft says Spain and the USA are the market leaders for CSP, and the solar market in general is growing. It is also evolving away from a situation where only developers dip into the CSP market, with more utilities getting involved as the market matures.
CSP market volume is predicted to reach €23bn in 2020 but Siemens has more ambitious plans: “Our target is to become the world's leading CSP vendor by 2015,” says Umlauft.
Strategy
As Umlauft sees it, one of the main strategies to enable Siemens' CSP business to grow going forward will be to drive down costs and to reach wholesale parity – i.e. the cost of producing solar electricity. He predicts that this could be reached in 6 years or longer depending on the location. In terms of sales, Siemens aims to reach over €1bn in revenue from its CSP business in five to 6 years.
The main strategy in place to achieve this is to optimise the system. As Siemens can now deliver 70% of a CSP plant inhouse, Umlauft believes it is possible: “That is what we would like to do – optimise the whole system from sun to power.
“Another important point is industrialisation by means of manufacturing,” he adds. “By automating and industrialising manufacturing, costs can be reduced. Looking back to the development of wind turbines, it took over 30 hours to produce a wind turbine two or three years ago, whereas now it is 16 hours on average.”
Umlauft expects similar development for solar power, but admits that the company does not plan to own CSP plants itself: “We are not going into competition with our customers.”
Lebrija
The Lebrija CSP power plant, located 60 km south of Seville, uses parabolic troughs and has an output of 50 MW. It has been developed as a joint venture between partners Valoriza and Siemens (through Solel). Construction started in the first quarter of 2009 and is scheduled to be connected to the Spanish grid on 1 January 2011.
Solel has over 25 years experience with CSP, as its predecessor built the CSP plant in the Mojave Desert in the USA. It is possible to produce CSP plants up to 250 MW but the Spanish Government has set a cap on 50 MW to qualify for the feed-in tariff.
According to Umlauft, costs for a CSP plant could be reduced 10%–15% by building a 250 MW plant compared to 50 MW. The cost for building a 50 MW CSP plant in Spain at the moment is €200–€250 million. But this could decrease to €150-€170m in 10 years time, he predicts.
Lebrija quick facts: |
|
Moshe Shtamper, Vice-President of Construction at Siemens Concentrated Solar Power, gave Renewable Energy Focus a tour of the Lebrija CSP plant, which has been built in a former cotton field. Shtamper describes it as “a swamp” and says this created extra construction challenges. The foundations, for example, had to penetrate an average 40 m into the soil to make the field stable enough.
The 1.2 km by 1.1 km solar field (around 150 acres) was built at Lebrija following instructions from the Spanish Government. A swamp is not the ideal site for a CSP plant and Shtamper admits it was a challenge to build an optical device on relatively unstable ground, but he says: “If we can make it here, we can make it anywhere”.
Constructing the plant
One challenge was to make construction firms realise the importance of precision when assembling a CSP field. Large structures such as roads and buildings need to be constructed with an accuracy tolerance of centimetres; when it comes to optical devices such as parabolic troughs, this margin is reduced to millimetres.
Both Umlauft and Shtamper believe industrialisation will be the key to the success of CSP and that every process involved when constructing a CSP plant should be industrialised and made simple. Compared to other CSP plant providers, Shtamper says Siemens has the advantage of already having a more industrialised construction process.
Siemens is currently developing a construction planning tool where developers can virtually build a solar field on a computer. This will again help with future construction of CSP plants.
It currently takes 15 minutes to assemble a parabola – one collector consists of 8 parabolas. Workers at Lebrija can assemble 48 parabolas in one day, which is enough for one ‘loop’, which is again connected to larger pipes bringing the oil to and from the power block. They have a special gripper designed to move and place the parabolas, which takes three people another 15 minutes to install.
All the workers at Lebrija are locals who have been trained by Solel/Siemens. Around 80% of the workforce is unskilled and the remaining fifth are skilled. It takes around 100 people to construct a solar field of the size of Lebrija and in general the CSP plant creates local jobs for unskilled workers.
Monitoring and operation
Lebrija has had WiFi installed to help monitor and operate the plant efficiently. Shtamper can sit in his office in Israel and check in real-time what is going on at the plant. In addition to CCTV, there are solar sensors on each driving leg feeding information back to the control room. These driving legs are mechanical, hydraulic machines moving each solar collector assembly (SCA) comprising 8 parabolas. The sensors allow the control room to adjust pressure on the pumps, the steam turbine and the output, according to solar radiation absorbed.
In case of servicing needs or severe weather conditions, the parabolas are moved to the stalling position – i.e. facing east as most of the wind in the area comes from the southwest. It takes 17 minutes to move the parabolas from west to east from when the signal is given from the control room.
As with most large projects, Lebrija had to undertake an environmental impact assessment. This was done before construction, has continued throughout the construction period and will be checked again when the plant is finished. This assessment is demanded by both the Spanish Government and investors.
For each finished loop, Siemens also performs quality checks using systems such as listening devices and pressurised air tests. When the field is finished, the company will run another test using pressurised oil.
Lebrija II and III have been designed, but are not yet approved under the Spanish royal decree necessary to qualify for feed-in tariffs. Without such a tariff, it is not possible to construct a CSP plant at present, says Shtamper.
Desertec
Siemens is heavily involved in the Desertec Industrial Initiative (DII), which was launched in July 2009 with the aim of creating the right conditions for implementing the DESERTEC Foundation concept in the EU, Middle East and North Africa. The joint venture was founded by 13 signatories.
DII's focus is on generating solar and wind power in the deserts of Middle Eastern and North African countries (MENA), and serving local demand and the European grid. DII will investigate and identify suitable technologies, as well the regulatory framework needed.
Although the project could meet up to 15% of Europe's energy demands by 2050, Siemens says it will also benefit the MENA area through knowledge transfer and the establishment of local industries. According to Utz, the energy exports would create a source of income for the region and renewable energy projects could provide power for desalination projects.
“We would not export [the solar energy] to the northern hemisphere if there is a shortage [on site],” he says. There are also several plans for solar power plants supplying the domestic markets in the MENA area.
Until 2012, DII will focus on creating conditions for viable business and investments for the EU-MENA Desertec project. Not only are there technological challenges to consider but also political and social parameters in many different countries and cultures. Umlauft says feed-in tariffs or other incentives for the power exported to Europe are needed.
“Would Europe be willing to prepare [itself] for renewable energy from outside the EU?” says Utz, raising the question of whether Europe would be willing to import renewable energy.
Transporting the energy
The main focus of Desertec will be solar power (80%) but it will also take into account other renewable energy such as wind and biomass. Umlauft says that all the relevant technology is already there, including the large transmission lines needed to transport the power to Europe.
According to Utz, it makes practical and economic sense to produce power where the resources are plentiful and then transport it to where it is needed. According to the German Aerospace Centre (DLR), Desertec would cost €400bn – €50bn for transmission and €350bn for the power plants.
Siemens has already been involved in long transmission lines such as the 1400 km lines transporting hydropower from Yunnan to Guangdong in China, and the Baselink HVDC (high-voltage, direct current) transmission between Tasmania and Australia. A small amount of power is lost in long-distance transmission but it is a very efficient process.
According to Utz, the framework for investment for the Dll project should be finalised in two to three years. Once investment is triggered, he says the timescale for the first Desertec installations will be clearer.