Wind on the Edge
In the past five years, some very inventive startup
companies have made a technological leap creating unique urban wind
systems that require no towers and fit in beautifully in urban and
suburban settings.
By Lyn Corum
Photo: AeroVironment
AeroVironment's wind turbine installation at Boston Logan
International Airport
Rising 50 stories above the Arabian Gulf, the twin towers of the
Bahrain World Trade Center offer a spectacular view of three spinning
wind turbines 29 meters in length, spanning the open space between the
two towers, gripping their sides, and holding them upright. Activated in
April 2008, the wind turbines provide about 15% of the building’s
electricity. The rest of the world will likely not be able to afford
such awesome wind systems, but, in the past five years, some very
inventive startup companies have made a technological leap creating
unique urban wind systems that require no towers and fit in beautifully
in urban and suburban settings. These urban wind systems rest nicely on
the parapets of multi-storied buildings, creating kinetic architecture
while reducing occupants’ power costs. We preview them here.
AeroVironment Wind Systems
The graceful metallic vultures poised at the edge of the tall
building will not take off and swoop down on unsuspecting critters—they
are actually AVX wind turbines manufactured by AeroVironment Inc. (AV).
They have already been installed at seven locations across the US, but
are not yet in full production, says Paul Glenney, the director of the
Clean Energy Technology Center for AV, based in Monrovia, CA.
AV’s first wind turbine, a rudimentary black box 4 feet by 4 feet,
was installed in June 2004 at Pioneer Electronics in Long Beach, CA,
says Glenney. “The intention was to understand the look and feel” of the
400-watt wind turbine and to quiz people about it,” he says.
From there, AV installed a beta system, this time a white box with a
screen, at a Staples Fulfillment center in Ontario, CA. Additional beta
systems were installed on buildings at BMW and Nestles, and also in
southern California. “We had increasingly more ambitious goals with each
installation,” says Glenney.
In the case of the BMW installation, the company had to get it
permitted, a difficult job involving several meetings with the city’s
planning commission. In southern California, some local regulations
require rooftop equipment to be screened or hidden—making a rooftop wind
turbine installation impossible.
The next step was a logical one. “We wanted to make it kinetic
architecture,” says Glenney. The current design, which AV has named
“Architectural Wind,” was created with the help of BMW’s DesignworksUSA.
In 2007, it won two international design awards. Since then, AV has
improved the turbine. The AVX400 was a three-blade, 400-watt unit, but
it created a lot of noise and was not cost effective. At 400 watts, it
would require 75 units to be installed on a building to get to 30 kW.
Installation costs alone made it prohibitive to commercialize. Back at
the drawing boards, AV added two blades and pushed it to 1,000 watts.
Thus, to get to 30 kW, only 30 units need to be installed. The
five-blade model also solved the noise problem. All the sites have now
been retrofitted with the 1,000-watt systems.
Glenney explains that the lowest speed most wind turbines spin at is
five miles per hour. The blades are made of molded thermoplastic with
carbon fibers. With the three-blade unit, they would start fluttering,
making a loud clacking noise when the breaking device went into action
at about 27 miles per hour. The new five-blade AVX1000 turbine not only
spins at low revolutions per minute (RPM), it takes a very high wind
speed to make it flutter.
AV has continued to work on the aerodynamics of its turbine, says
Glenney, in wind tunnels at California Institute of Technology and
Oregon State University. This wind turbine is designed to take advantage
of the chimney effect of rapidly rising wind or “accelerated wind zone
movement” coming over the top of a building at strength 40% greater than
the prevailing wind flow, he explains. Knowing the vector flow, the
turbine can be positioned at the edge of a building to catch that faster
wind.
Glenney says AV might decide as soon as the third quarter, 2008, to
go into production, or it may decide to stay in low production for
another six months. It will depend on adoption by customers, and whether
the company can reduce manufacturing costs, he says. The company wants
to retain the aesthetic design, but to reduce the price 30%, it may look
at smoothing out blade curves, or it may be able to leverage economies
of scale, he says. The current high commodity costs could impact
manufacturing costs, but not at the current low-rate of production, says
Glenney.
The public is experiencing tremendous interest in AV’s turbines.
Glenney says the company does have orders, and if it can create
aggressive cost reductions, it may move forward. Visit the company’s Web
site at www.avinc.com
for news and more details.
AV Wind Turbines Attract Attention
Tom Romundstad, St. Louis County, MN, property manager in Duluth,
can attest to the popularity of AV’s wind turbine. Six 1-kW units were
installed on the roof of the Government Services Center in Duluth early
in 2008. Since then, Romundstad has received calls from Montana, Alaska,
Wisconsin, and many other municipalities inquiring about the units,
following local press coverage. And the local National Guard wants to
install some on its building.
Romundstad explains that St. Louis County bought the 1980s era
building from the State in 2002. It was in poor shape and used a lot of
energy. Since then, the county has completed a large number of retrofits
including lighting, and the rebates awarded for the energy conservation
work were reinvested in solar photovoltaic systems on three buildings
including this one. The turbines complement the solar, he says. The
system, which is scalable, currently powers the building’s hallway and
stairwell lights.
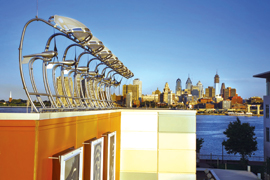 |
Photo: AeroVironment
AeroVironment's Architectural Wind turbine installation at the
Aquarium in Camden, NJ. |
The turbines were installed on the east edge of the rooftop to catch
winds coming off the north shore of Lake Superior. A support I-beam was
lifted to the roof on which the turbines were mounted. This will allow
the roof to be re-roofed later on, explains Romundstad. The turbines can
turn 35 degrees in each direction to catch the wind. He says AV now has
turbines with 360-degree access to the wind.
The county did not need permits to install the wind turbines, but
Romundstad had protective guards placed on top of the turbines in case
falcons, which nest in downtown Duluth, come by to visit. Since the
system was installed, the area has experienced a lot of west winds.
“We’re in the period now when northeasterly winds pick up,” he says,
explaining one of the reasons why the turbines have produced just 400
kWh since installation.
The major reason for the lack of production, however, was the
shorting out of two generator-housing seals shortly after installation
last February that reduced power production on the 6-kW system by 2 kW.
The lack of production was not noticed for several weeks. As soon as AV
was notified, a repairman was dispatched from California, and he took
all six turbines apart, checked all the seals, and replaced the
destroyed ones.
In addition to St. Louis County, 20 Architectural Wind systems were
installed in March 2008 at Boston Logan International Airport, MA, on
the roof of the Logan Office Center. The wind turbines are expected to
provide about 2% of the building’s monthly energy use, or $13,000
annually.
Other locations include Laughlin Air Force Base in Texas, where six
wind turbines were installed on the roof of the Laughlin flight
simulator between summer 2006 and December 2007. A series of wind
turbines were installed at Arizona State University, in Tempe, AZ, on
the edge of the building housing the School of Sustainability, in early
2008. And a 4.8-kW wind turbine system was installed on the roof of the
Adventure Aquarium in Camden, NJ, in September 2007. Finally, Kettle
Foods installed 18 Architectural Wind systems on the roof of its new
73,000-square-foot potato chip manufacturing facility in Beloit, WI, in
mid-2007 as part of the company’s effort to build sustainably. Kettle
achieved gold level certification for Leadership in Energy and
Environmental Design (LEED) from the US Green Building Council. AV
reported the 18 1-kW wind turbines are projected to generate
approximately 28,000 kWh annually—enough to produce 56,000 bags of
potato chips, according to Kettle.
Broadstar Wind Systems
Likening the AeroCam to a mini ferris wheel, the small wind turbine
could generate electricity in an urban setting like a shopping mall and
become an architectural attraction, says Steve Else, president and one
of the founders of Dallas, TX-based BroadStar Wind Systems. He believes
the AeroCam can easily be installed in almost any environment to create
distributed power generation sources.
“I think this market will explode,” he says.
Broadstar started up in 2004. Following years with Oracle and Ariba as a
manufacturing systems engineer, Else started an oil and gas investment
company in 2002 and is using the profits to fund this company. Tom
Stephens, the company’s chief engineer, is the inventor of the AeroCam.
The AeroCam is still in the testing phase, so Broadstar will seek
financing starting in summer 2009 once beta testing is concluded, around
the time when the company will go for general deployment of the wind
turbine.
“We won’t go to general release until we iron out all the issues,” says
Else. “It’s very important to us that customers are happy and the
product is reliable.”
Beta testing with 10-kW and 250-kW prototypes is beginning in at least
five different environments. Two are at Fortune 100 company locations at
an industrial complex and in a one million square foot distribution
center. Else says the second beta test will begin at Texas A&M
University, in July. Another will take place in the United Kingdom on an
eastern shoreline, to determine how the blades deal with salt blast and
corrosion. He is looking for a test site in Canada to check out how the
AeroCam handles icy conditions.
The patented design features 10, 12, or 14 blades on each module,
depending on the size. The blades use the natural flow of air to create
lift, and an offset cam that allows the blades to continually adjust for
optimal pitch throughout a 360-degree rotation of the turbine. The
AeroCam is about 30% smaller than a conventional horizontal axis wind
turbine yet generates the same amount of power. The original module
produces 10 kW at 30 miles per hour wind speed. The company is designing
100-kW, 250-kW, and 500-kW models in parallel. In each of the models, as
wind speeds increase, delivered power also increases. For example, the
power curve on the company’s Web site, www.broadstarwindsystems.com,
indicates the 500-kW AeroCam IV will produce 800 kW at 35 miles per
hour.
The AeroCam will fit in environments where big turbines won’t fit, says
Else. In the urban setting, the roof edge of a tall building is a
perfect place for a small wind turbine, he argues, given that the focus
of the wind is at the building’s parapet. Currently, there are no
standards, and no permits are required for the 10-kW AeroCam, which has
a 10-foot diameter. Else says this model may fall within the category of
rooftop accessory requirements.
Ideally, the AeroCam lends itself to being integrated into the design of
a new building. Else predicted that in 10 years, all new buildings will
integrate solar, wind, and a ground loop to cool liquid underground for
air-conditioning. “Sensibly designed buildings should have all three,”
he says. Else says the urban sites won’t be the biggest market
initially. He predicts it will take four to eight years to achieve a
large urban market, and must be done in collaboration with others in the
industry. Other applications, including micro-wind farms, require less
real estate than traditional wind systems since they can be installed on
poles as low as 30 feet. Small communities or rural cooperatives could
install a series of modules at the edge of a park and interconnect with
the local utility. The AeroCam requires no special equipment or cranes,
making it easier and less expensive to install and maintain over the
long term.
The AeroCam can also be installed as infill in large fuel storage
sites or in existing wind farms to create greater overall power
generation. There is plenty of wasted land in between big wind turbines,
which must be placed three diameters apart hundreds of feet above the
ground to operate in smooth airflows, Else points out. The AeroCam can
withstand turbulent environments because of its lower hub height and
small footprint, and capture surface-wind energy without disrupting the
airflows that the larger turbines need to operate effectively.
Else says cost modeling indicates the company will be able to
manufacture the AeroCam at $1 per watt, allowing a customer to buy a
250-kW unit for $250,000. He says the turbines would be manufactured in
the United Kingdom while sourcing components from Asia and China. The
small, modular size of the AeroCam will allow the company to ship it
anywhere in the world for $4,000, he says.
Aerotecture Wind Systems
Aerotecture International’s unique and patented wind turbine design
resembles a giant squirrel cage, except for the blades whirling silently
inside. The cage can be installed either horizontally or vertically. It
is small enough that two men can carry a unit and tip it up for vertical
installation. This can be seen in a documentary on the company’s Web
site, www.aerotecture.com. Bill Becker, the coinventor and CEO of the
company, talks while leaning against an horizontally mounted
installation as the blades whirl.
A company representative was not available to talk about its wind
turbine system, communicating that they were overwhelmed with media
inquiries and work, but information is available on the Web site. Also,
two owners of systems describe their experiences below.
The Aerotecture wind turbine comes in two models: The 510V is rated at 1
kW in 32-miles-per-hour winds; the 520H is rated at 1.8 kW. The newest
model is a hybrid, using solar panels in tandem with the 510V model. The
company recommends the units be installed at least 40 feet above the
ground to take advantage of strong winds, and that they be above or away
from surrounding trees and other obstructions, and in an area where the
average wind speeds are at least 10 miles per hour.
Vertical Aerotecture wind turbines operate in winds coming from all
directions, but horizontal systems require a dominant wind direction for
maximum efficiency. The rotational axis must be oriented perpendicular
to the dominant wind direction. The corkscrew design of the
polycarbonate foils tipped with aluminum blades shields the turbine and
helps it start at very low wind speeds of two miles per hour.
This feature also protects birds. At the Randall Museum in San
Francisco, CA, where an Aerotecture wind turbine was installed in June
2005 to power an exhibit for the United Nations World Environment Day,
there was not a single bird killed. There are 100 bird species on the
hill where the museum is located. “We watch birds fly around it, like
red tail hawks,” says museum director Chris Boettcher. Apparently, they
see the glint of the foils that reflect light 360 degrees, he says.
All Aerotecture turbines are commercially available, and are designed
and custom-built to fit the architecture of the building. The
electricity generated by the wind turbine system can be sent to a
battery bank or to the utility grid. The 510V model costs about $15,000,
and the 520H model costs $21,000. Currently, the wind systems are only
being sold in San Francisco; Chicago, IL; Paterson, NJ; and upstate New
York where the company has dealerships. Aerotecture is currently
focusing on grid-connected systems where utilities provide net metering,
according to information on its Web site. It is working to set up mass
manufacturing and dealerships in other areas of the US and worldwide.
The first Aerotecture turbine was installed on the roof of Becker’s
cousin’s law office in Round Lake, IL, in October 2003, where it
operated as the test site. Becker’s cousin, Jim Magee is the senior
partner of Magee Negele & Associates, and the Round Lake village
attorney. In that role, he was able to expedite the city permits for the
installation on top of the one-story office building.
“In fairness to truth, there’s been so much experimentation,” says
Magee. Primarily, this has involved upgrading the alternators. The first
was a converted automobile alternator and the newest one is a
much-improved technology, he says.
The greatest benefit, Magee says, is the backup power it provided the
two times the utility power failed. The turbine’s generated power is fed
into the back office and powers computers and lights through batteries.
There was no flicker in the seconds after the power failure—“It was
dramatic and wonderful,” he says.
The original battery set is still operating, and, when they are full,
the utility meter does run more slowly. “They’ve been up there,
virtually silent, except when huge winds produce a slight sound,” says
Magee.
He also says that there is no vibration and no bird kills, even
though the cage is open. It is noteworthy, he says, that the turbine is
not bolted or anchored to the roof. Six cinderblocks are at the base,
and the turbine could be picked up and moved, cinderblocks and all.
The one disadvantage Magee described is that it is only 12 feet off the
ground. If it were over 30 feet it would be better. Furthermore, trees
are on two sides that block some wind. “Higher and more open is
desirable,” he says, which would produce more consistent winds.
Larry McCarthy, regional vice president of property management for Mercy
Housing Lakefront, Denver, CO, says the jury is still out on the eight
520H Aerotecture wind turbines that span the front edge of the
five-story, 96-unit Margot & Harold Schiff single-resident housing
development in Chicago. Grants from the city and state paid the $150,000
cost of the system and installation. The building is new and the wind
turbines are building-integrated. The architect, Murphy/John Architects,
claims the geometry and orientation of the building was designed
especially to increase the speed of the wind as it flows over the roof.
The eight wind turbines were installed on the edge of the roof in August
2006 and began operating in March 2007. It was the Aerotecture’s first
battery-free installation.
McCarthy hadn’t yet arrived on the job when they were installed, but he
says the alternators have been malfunctioning, and they are just now
getting a meter to measure energy use. These turbines were the first to
be installed horizontally. “We’re not getting movement when the winds
don’t blow in the right direction,” he says. “I would have standing
turbines if we were doing it again.”
McCarthy explains that the power generated by the turbines goes directly
into the building’s electric system. A solar thermal system was
installed at the same time and heats water used by the residents. He
says the company that was hired by Aerotecture to install the turbines
handles maintenance on the system. McCarthy’s advice to potential wind
turbine buyers: Do your homework and investigate the cost to maintain
the system.
The projected energy savings for this system was $1,500 per year. At
that, the payback is something like 50 years, he says. The new meter
coming will either prove or disprove that.
Blue Green Pacific
Blue Green Pacific, based in San Francisco, has designed a residential
wind energy system that would also be appropriate for small businesses
and schools. Blue Green’s 500-Watt turbine is a vertical helix design
offering a small footprint, minimal noise, no threat to wildlife, and is
affordable. It can be viewed at the company Web site,
www.bluegreenpacific.com.
Tod Pelman, CEO of the company, says development is still very early, at
the alpha level. Beta level testing is just beginning and will continue
for six months. The company is also developing a 1-kW model. Two units
have been installed on residences (including his) in San Francisco. Two
other units have been installed on a commercial building and on a
school.
San Francisco is developing permitting rules for urban wind systems,
propelled in part by Blue Green’s installations. It created an urban
wind task force to look at whether or not a particular environment is
conducive for wind turbines, according to Johanna Partin, renewable
energy program manager for the city. The task force will work with the
Building Inspection and Planning Departments to develop the rules.
Partin says Blue Green’s three wind turbines installed on the two
residences were permitted on a one-year pilot basis, and they have to be
Underwriters Laboratory (UL) listed. She says all vertical axis turbines
are in the process of getting this listing.
Motorwind
Lucien Gambarota who invented and developed motorwave technology and,
more recently, the motorwind system, founded Motorwave Group, based in
Hong Kong. He did not provide an interview, and the following
information was developed from the company Web site,
www.motorwavegroup.com.
Motorwind microturbines look like a grouping of children’s colored
whirling pinwheels lined up on a post or along a fence. Furthermore,
they are truly renewable. The 25-centimeter, round compact gearwheels
with blades made of plastic can be arranged in a range of shapes and
sizes from two to thousands of square meters. Because the blades are
injection-molded from polypropylene, the microturbines can be recycled
several times. They are designed to be installed anywhere on any support
in modules, and they operate at low and high wind speeds ranging from
two meters per second to more than 10 meters per second.
The company is targeting applications for homes, factories, companies,
schools, and farms. The first commercial installation was on the roof of
the Hong Kong Sea School in January 2007. The 396 turbines were stacked
six rows high in three sections and were colored to spell out the name,
“Sea School.” Each unit is rated at 125 Watts. Average output was
predicted to be in the 0.6 kW to 1.3 kW range with a daily production of
approximately 10 kWh to 30 kWh.
The company is recommending the Motorwind microturbine produce power
only for in-house use at this time. Currently, it does not have the
regulators necessary to interconnect with the grid. Motorwind
microturbines are available in an 8-turbine set for high wind speeds and
a 20-turbine set for low wind speeds.
Motorwave does not have distributorships outside Hong Kong, but the
microturbines can be ordered from their Web site. The cost is
approximately $4.00 per watt with a minimum investment of
$200.
Author's Bio: California-based Lyn Corum is a
technical writer specializing in energy topics.
© Copyright 1996-2009 Forester Media, Inc. To subscribe or
visit go to:
http://distributedenergy.com
|