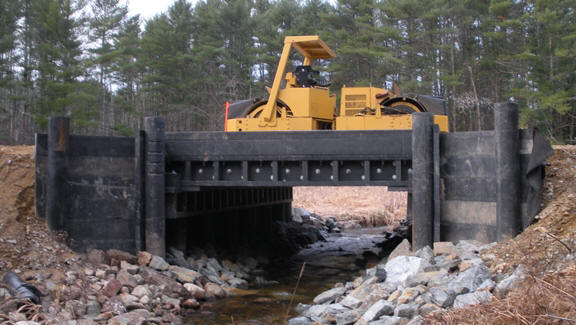
Construction in Europe is traditionally associated with metal, steel and other heavy materials, but plastics and plastic composites are increasingly used as energy and cost-efficient alternatives for buildings, bridges, houses and other structures.
Construction accounts for more than 20% of demand for plastics in Europe, the second largest market segment after packaging, according to PlasticsEurope in Brussels.
Plastics have long been used by builders for seals, windows and doors, pipes, cables, floor coverings and insulation, but innovative companies and engineers see much greater potential across a wider range of structural and other applications.
Indeed, plastics and composites present an opportunity to create more sustainable structures as their moisture resistance means they do not rot or rust or need regular re-painting. They are strong and durable, lightweight, easily transported and quickly installable.
"Just like public authorities, architects and construction as a whole are increasingly looking at sustainability as the main criteria for new-generation building," says Thomas Bauwens, spokesman for PlasticsEurope.
"The sector is now looking at energy and resource efficiency, along with reduced CO2 emissions, as the main challenges for future buildings. This is true for the whole world; especially developing countries."
He notes that plastics are now being used in new buildings for everything from weather-proofing, coating and insulating facades, gutters and drainpipes, roof insulation, draft-proof and energy efficient windows, doors, inner walls and cellar insulation, water pipes and cables insulation to heat recovery and ventilation systems.
"One cannot imagine a passive house or even an energy efficient house not using plastics to ensure the highest energy and resource efficiency," he says.
Emerging trends include innovative applications by moulders, companies and engineers who are not just integrating plastics into construction but making it their primary material.
"Plastic alternatives to asphalt and concrete, made of recycled plastics, already exist and provide better energy and resource performance than these traditional materials," says Bauwens.
A pedestrian overpass made of a composite lattice structure was erected in Moscow, Russia, in March by ApaTech, a local specialist manufacturer of composites products. The overpass consists of four 33m spans integrated into a single unit at a centre support, with four vertical towers at each extremity containing pedestrian staircases.
The decorative spiral lattice is made from glass-fibre reinforced plastic based on multiaxial quasi-isotropic fibres and polyester resin. The total weight of the composite elements is 13,689kg: a similar metal structure would weigh 38,447kg.
Europe's first recycled plastic bridge was erected near Edinburgh, Scotland, in December 2011. At 27.4 meters long, it replaced an old steel and timber road bridge across the River Tweed. Built in sections by Axion International Holdings, a U.S. profiled by Waste & Recycling News earlier this year, from a 100% recycled structural composite, it was shipped to Scotland then erected in less than two weeks; a fraction of the time taken for more traditional materials.
William Mainwaring, co-founder and CEO of recycled plastics manufacturer Vertech, based in Wales, Axion's project partner for the Scottish bridge, says: "The potential for plastics - both virgin and recycled - in construction is considerable. Many of Europe's main contractors and their consultants are looking for alternatives to conventional materials."
Vertech, which makes sheets, profiles and structural components, has since fielded enquiries from leading construction sector clients, contractors and engineering consultancies. Mainwaring concedes that the general public and some companies may once have been reluctant to see plastics as building materials on a par with metal or steel in terms of strength, durability and other characteristics. "But attitudes are already changing rapidly," he says.
As European Plastics News reported in May, Acciona Infraestructuras of Spain has won recent industry awards for two projects: a composite pedestrian bridge-beam made from a resin infusion of carbon fibre with epoxide resin; and for the world's longest stress ribbon bridge, which uses wound, unidirectional solid carbon fibre cables as the primary load-bearing supports.
There is considerable R&D activity. For example, pultruded profile maker company ICCO Composites, based in France, is participating in France's DECID2 smart composite materials project to install a 20m long footbridge on a technology campus in the Pays de la Loire region. The demonstrator project will have optic fibres and ultrasonic sensors embedded into the bridge's composite profiles to monitor deformation and flag up warnings in the case of a structural failure.
Prime, a European Union project funded under its Seventh Framework Programme, aims to develop cost-effective, flexible moulding technology to manufacture high value, complex, recycled polymer products with similar or identical mechanical properties to virgin polymer, metal or timber alternatives.
The opportunity is multi-material, according to Thomas Bauwens. While PVC is the most widely used plastic in construction, other common polymers are medium and high density polyethylene and polystyrene.
"Each has specific strengths: it all depends on the application," Bauwens says. "1.6cm of plastics foam replicates the insulation of a 1.3m thick concrete wall. Installing 80 million plastic window frames in Europe would eliminate the need for five nuclear power stations. Plastic window frames can last over 50 years and plastic pipes almost 100."
The British Plastics Federation trade association reckons plastics offer opportunities for innovation and growth through techniques such as prefabrication, which moves work away from construction sites to factories for pre-assembly and then easy transport, such as in the Axion/Vertech project.
The opportunity is enticing to an industry pondering where future growth will come now that it has clawed back ground lost in the financial crises.
Bauwens says: "Europe is one step ahead when it comes to green technologies in building and construction and the plastics industry is no exception - thanks to continued innovation, we are optimistic about the future."
M J Deschamps is a reporter for European Plastics News, a sister publication of Waste & Recycling News.
w w w . w a s t e r e c y c l i n g n e w s . c o m
copyright 2012 by Crain Communications Inc. All rights reserved.