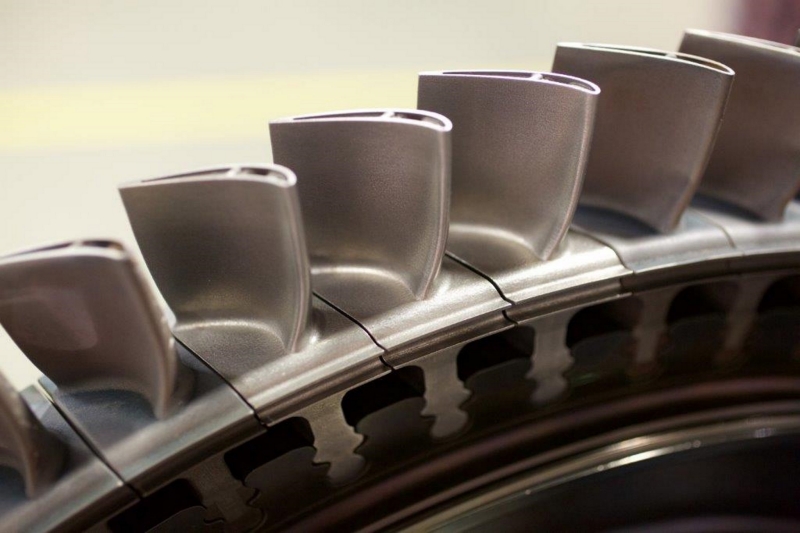
By Editors of Power Engineering
Siemens announced it has successfully tested power generation gas turbine blades produced entirely through metal-based 3D printing, also known as Additive Manufacturing.
The blades, tested under full-load engine conditions at 13,000 revolutions per minute and temperatures above 1,250 degrees Celsius, were produced by Siemens subsidiary Materials Solutions. Siemens purchased Materials Solutions, which specializes in high-performance parts for high temperature applications in turbomachinery, last year.
The tests were conducted at the Siemens testing facility in the industrial gas turbine factory in Lincoln, UK, using a Siemens SGT-400 industrial gas turbine.
In 3D printing, a digital design is fed to a machine that “prints” thin layers of material one at a time. Though 3D printing at the consumer level is frequently done with plastics, Siemens’ blades were made from the powder of a polycrystalline nickel superalloy, and designed with a cooling internal geometry to increase the overall efficiency of Siemens gas turbines.
"This is a breakthrough success for the use of additive manufacturing in the power generation field, which is one of the most challenging applications for this technology," said Willi Meixner, head of Siemens' Power and Gas division.
No commercial production date was given for 3D printed turbine blades, though Meixner said 3D printing reduced the lead time for prototype development by 90 percent. The company now uses 3D printing extensively for rapid prototyping, and has already introduced serial production solutions for compressor and combustion components in gas turbines.
Copyright © 2007-2016. PennWell Corporation, Tulsa, OK. All Rights Reserved.